Dehumidification and Drying Concrete: Hurrying Up the Wait
In flooring applications, either finished concrete or applied flooring, there is always a “hurry up and wait” element – wanting to move ahead but knowing that rushing too quickly may result in a flooring failure or flooring problem. Meeting concrete and flooring specifications can seem to be a luxury that is not always available to the contractor on a tight schedule.
Dehumidification is one of the processes often used to try to encourage a concrete slab to dry more quickly in order to reach the installation point. The basic concept is simple: reduce the dew point of the air surrounding the slab so that more of the latent moisture within the slab can evaporate out through the slab surface. In the building industry, there are several common approaches to dehumidification: condensation dehumidification, heating (or drying) dehumidification, and desiccant drying.
Desiccant-based dehumidifiers use a chemical attraction to remove moisture from the air. Humid air is moved across a desiccant material that binds and holds the moisture. A hot air stream is then used to release the moisture from the desiccant and vent it away from the slab’s environment. The dried desiccant then absorbs more moisture and releases it again through heating in a continuous process. This process is not influenced by external weather so can be used year round as long as the concrete slab can be isolated from weather conditions.
The condensation process uses cooling-based dehumidifiers which cool air, effectively dropping the dew point so that moisture can be collected and drawn away. By contrast, dehumidification uses heated air to raise the dew point of the surrounding air, allowing it to absorb more moisture from the slab surface. The saturated air is then circulated, either through a collection system or to the outside air where it releases the excess moisture as it cools. It should be noted here that most installed HVAC systems are not capable of removing the amount of moisture emitted through the drying process of a concrete slab. While it may be possible to raise or lower the ambient temperatures through the HVAC system, dehumidification must actively remove the excess moisture from the structure. If the moisture is simply moved around within the walls, excess moisture can cause mold growth or equipment deterioration over time.
The real key to successful dehumidification is to have the concrete slab completely enclosed so that the moisture removed during the process is not re-introduced to the slab’s environment. Either the slab must be enclosed in service-ready indoor conditions, or a vapor barrier must be erected around it for outdoor conditions. Accurate relative humidity (RH) testing lets you accurately track the movement of moisture out of the slab. Once the slab has reached the desired RH levels and the finish or flooring is applied, the concrete will be optimally able to sustain a quality finish that will last for years.
Wagner Meters’ Rapid RH® moisture testing system can help you easily and accurately test the RH so you can track the moisture out of the slab during the dehumidification process. Since 2002, ASTM-F2170 in-situ RH testing has been replacing calcium chloride as the preferred method for concrete moisture determination.
Call Wagner today at (541) 291-5123 or order your Rapid RH® moisture measurement system online.
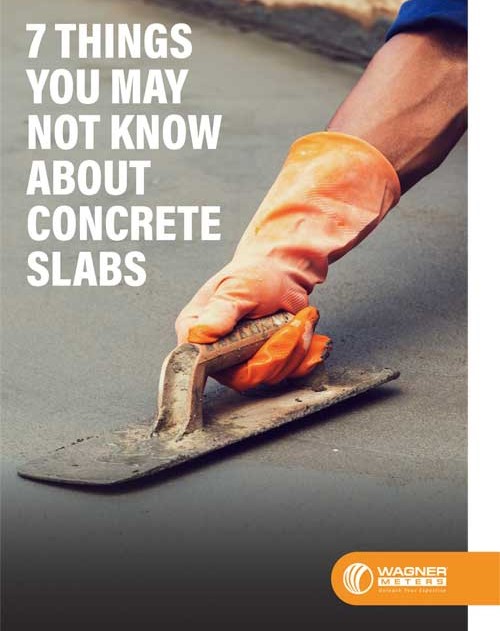
Free Download – 7 Things You May Not Know about Concrete Slabs
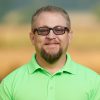
Jason has 20+ years’ experience in sales and sales management in a spectrum of industries and has successfully launched a variety of products to the market, including the original Rapid RH® concrete moisture tests. He currently works with Wagner Meters as our Rapid RH® product sales manager.
Related Posts via Taxonomies
Last updated on October 1st, 2021
My situation is a foundation wall leak in the basement. The water made its way under carpeted and padded floor. All flooring has been removed and currently we have a box fan and 35 pint dehumidifier working in the area (approx. 700 sq. ft. basement area thats walled off and finished with the wet concrete floor area being 10′ X 14′). The current temperature in the basement is in the 70’s.
Do I need an additional heat source to bring the temperature up even higher?
Is a box fan good enough for moving air in the effected area? (approx. 10′ x 14′)
Do I need to put up some plastic from floor to ceiling to section off the 10′ X 14′ wet floor area ?
Is my dehumidifier big enough?
I understand this will take a few months to dry but I want to make sure I’m setting up the proper conditions for success.
Thanks
Albert:
Thanks for the email. If you are staying consistently in the ’70s, you should be fine. I would want more air movement than a single box fan, but I can really recommend a size or velocity. I would personally want to separate the damaged area from the undamaged area to ensure I limited exposure. As far as the dehumidifier, that question is best answered by what RH% is the dehumidifier able to maintain in that area? The lower the RH% the better. If it is in the 30-50%RH range consistently, then you are probably good. I hope this helps.
Jason,
I own a 700 s.f. condo that is one of 8 condos ground level in a single structure. The condo has experienced 3 slab leaks in 2 1/2 years.
I now am unable to lay down flooring due to high levels of moisture in certain areas since April 2021. Living room is approx 6.095 pounds per 1,000 s.f. in 24 hours, but dining room is at 25.042 and walk in closet is at 34.986. This with area being uncovered for 4 – 8 weeks. (Some area uncovered since April)
I have closed off areas using dehumidifiers 24/7 last two weeks numbers in walk in closet went UP and dining room went down slightly.
What can be done to dry out the slab?
Do you suspect that there may be another leak that has not surfaced yet. Possibly under another unit?
In all the excavations I did not see any signs of a membrane. Any insight would be appreciated.
Thanks for the question and sorry about the problems. With a slab that has no membrane under it, you may temporarily “dry” it out, but there will always be the potential of moisture gaining access through the soil, whether there is a plumbing leak or not. I can honestly say I have never seen or heard of a CaCl2 test reading in excess of 30, so that is interesting. You should investigate some type of topical moisture mitigation system to minimize the moisture that comes in contact with the finished floor product once installed. Makes sure to read the fine print and make sure the product is acceptable to be used on slabs with no moisture retarder below. Good luck.
This is an outstanding post that’s filled with so many useful nuggets. Thank you for being so detailed on dehumidification and drying concrete: hurrying up the wait.
Thanks for sharing the tips. I am using this to make others understand
Hi Jason. We had a concrete and screed mixed poured on top of our ufh (35mm worth). Our builder recommended we wait one month before putting our new carpets down, but we are four days away from that mark and we can still see dark patches at the surface level – compared to other, light grey blotched areas. I did a moisture test (using an apparatus I bought online) but I can only measure the surface level which is coming up at 1.0%, even on the darker spots. We own a basement flat and have not been living in the property, so the windows are not open all day to air anything out. What would you suggest we do to speed up the drying process?
Victoria:
Thanks for the question. The best conditions for drying will be consistent temperatures, air movement across the surface, and low humidity in the air. So getting the ufh going, fans moving air, and potentially some type of dehumidification would be your best bet. Good luck.
Hi Sir,
I am acting as an appraiser for a residential policy holder that had a water leak on 3/1/20. The opposing appraiser had the slab tested on 3/4/21 ( a year later) as he hypothesized there was another leak. Leak detection indicated there was no additional leak. I do water mitigation as well, but have only dried a slab once in my fourteen year career, probably 12 years ago. I recall this taking around 2 months to dry. With a desiccant, floor mat system, and air movement how long do you suppose drying would take? Also, I imagine its similar to other materials in that the longer a concrete slab has been wet, the longer it takes to dry, is that correct in this case?
Thank you in advance for your time!
Brad Hall
Brad:
Thanks for the questions. The answer to you first question is, it depends. How thick is the slab? Was the water from the top down or the bottom up? How wet is it? How dry does it need to be? If the leak was from below, is the “wetness” in an isolated area? If not, is there no vapor barrier below the slab? In general, if you are looking at a finite amount of moisture to dry from a slab, it will take 30 days for every 1” of slab thickness to reach around 85% RH, internally. Yes, you are correct that the longer the water sits on a slab, the more it will absorb, and the wetter the entire mass will become. Good luck.
Hi,
My company is in the process of building a new temporary building.
Currently the concrete has been laid but the walls are not up yet, because of this water is accumulating on the concrete.
Do you know of anyway that we can remove or absorb the water ?
Thank you
Stephanie:
Thanks for the question. The most common way to take care of this is to get a floor squeegee like this
https://www.northerntool.com/shop/tools/product_200416624_200416624?cm_mmc=Bing-pla&utm_source=Bing_PLA&utm_medium=Cleaning%20%2B%20Janitorial%20%3E%20Mops%20%2B%20Squeegees&utm_campaign=Libman&utm_content=132396&gclid=8596dccdf620186619cbbcd5ded96a3a&gclsrc=3p.ds&msclkid=8596dccdf620186619cbbcd5ded96a3a
and periodically squeegee the water. Not the most glamorous, but it is effective. Good luck.
1 month ago had a leak in the cinderblock from water main. A hole was put in the outside wall to repair. It was covered by us temporarily pending insurance etc.
We initially had a mitigation company treat the area and it dried but rained afterward and wet again we believe. Mitigation refused to redry due to insurance payment problems.
We bought a 50 pint dehumidifier and it is removing water. The area is getting smaller.
Humidity in room down to 28 we live in Florida.
It still has areas in the 90s. Is this a normal speed?
We had a slab leak surface 12/21 & repaired on 12/22, pinhole in 3/4″ cold water line, below our grade level slab confined to one room. Not sure how long the leak had been present before the water showed up under the carpet. We have removed all carpet and padding from the room and are using dehumidifier, heater and fan to attempt to dry slab. On a moisture meter the slab in most of room reads 100% moisture level. First question is would there be any way to better expedite the drying process and if not is there a way to gauge how long it might take to get the moisture level to a point where sealer could be applied? The restoration plan is to install a moisture proof underlayment below a vinyl plank flooring surface.
John:
Thanks for the questions. First, the flooring industry, in general, doesn’t recognize surface moisture meters for making installation decisions. With this, it makes it hard for me to interpret your 100% reading. I would consult the flooring manufacturer that is being installed and find out what type of moisture testing is required to maintain a warrantied installation. Once you have done this testing, then you can gauge how much drying needs to be done. As far as how long, I cant give you a definitive, but I can say it sounds as if you are taking the right corrective steps. Good luck.
I live in a basement…I have mine on day and night alt 50%…my question is…is it healthy…does the dehumidifier will rid of water of your body also? I notice that my skin is getting dryer and dryer every time.
Hi Jason,
We have a slab we are trying to dry for a wood floor installer. He would like MC to be /b/ 3-3.5 on a concrete moisture encounter meter (0-6 on scale). Slab was exposed to water damage for 3-5 days. It is contained in one room. We tented the slab and used a desiccant to dry. There was no movement in the MC of the slab. We removed the moisture barrier and installed infra red heat lamps coupled with dehumidification. MC went down a full point on our concrete encounter meter but has plateaued. We are on day 20 of drying. This past weekend, I turned off the heat lamps for two days (dh still operating with decent grain depression). After turning off the lamps, we gained a point to point and a half (4-4.5) of drying but the second day after the lamps were turned off, the MC went back up. I take it as positive info that moisture is moving in the slab. Is there any thing different we could do to push it over the top to obtain the dryness the installer is seeking?
George:
Thanks for the question. Its sounds like you are doing quite a bit. I would be curious to know what the RH% in the tent is during application of heat lamps and then during that 48 hours after you turned them off. Anyway, the only additional thing I could recommend would be a high level of air movement across the slab although that may be difficult with tenting. Good luck.
Jason, my garage was turned into a regular bedroom 30 years ago. The garage flooded with 3 inches of water in September. i just a few places water comes up when I don’t have the ac on. When I turn on the eater it comes up more. which should I use? ( to dry out in order to put a sealer on), moisture only comes upin one certain area, but still smells like musty. What to do. Thanks
Helen:
Thanks for the questions. Probably your best bet is to have consistent, reasonable heat in the environment. Additionally, I would add some type of dehumidification unit to the area so when the moisture comes up, the air has the ability to absorb it and take it away. Obviously, at some point you will then need to moisture test to see just “how bad bad is” in order to pick the correct sealer. Good luck.
Hi Jason,
We poured a 150mm thick slab on ground with vapour barrier underneath in May 2019 and have tested the RH% last week (around 120days after pouring) and it is around 85-90%. Our flooring contractor has advised we require a moisture barrier installed and 3mm topping prior to vinyl floor install.
Can you please advise whether this would typically reduce over time and how to prevent/prepare for future slabs so we can try get the RH% around 75% so a moisture barrier is not required?
Thanks in advance.
Jason:
Thanks for the question. Keep in mind, “days after pour” plays into the drying equation very little. The biggest part of the drying equation is “how long has the building envelope been enclosed and air conditions been conducive for drying?”. Getting the envelope closed, consistent reasonable temperatures, and low relative humidity in the air will expedite the process. Getting the slab to 85-90% in the time period you have outline is actually pretty good. I would be curious though why the vinyl/adhesive limits are so low. I typically see 80%+?
Hi Jason,
Please help. My disabled mother lives in a flat which is on the 3rd floor and has concrete floors. The flat below had a leak in their ceiling a few years ago which apparently was the pipework between the 2 flats i e above their flat and below my mother’s. My mother also had a leaking shower for some time. The bathroom floor was drenched when the vinyl was lifted 3 weeks ago, she has had a dehumidifier, heater in it now for 2 weeks and the damp meter reading is still coming up at 99.9%. Please could you advice the quickest way to dry the concrete floor in the bathroom?
Thanks Sandy
Sandy:
Thanks for the question and sorry for the issues. Assuming whatever caused the issue has been fixed, heat and dehumidification are the biggest keys to drying. I would make sure the damp meter is a good quality device, representing information that will help make a decision on when the floor is dry. Many out there aren’t. I would also make sure the dehumidifier is actually big enough. The easiest way to do that is to get a device to measure the relative humidity and temperature in the air. With a properly functioning dehumidifier, the relative humidity should be low. Good luck.
Hi Jason… Thanks a lot for the writing and for all these answers.
We installed a WarmUp floor heating system in a very small amount of self-leveling concrete(1/4″ thick). Underneath this layer there is a concrete slab covered in plywood and a thin layer of paper that was left from removing some old linoleum, I would assume there is also some glue between paper and wood.
On top of this, we are trying to install a terrazzo tile floor. The installation instruction from the tile manufacture are very precise and indicate a max humidity in the slab of 4%, that sounds quite low to me and hard to achieve when I read numbers online, a lot of people say with 8% humidity its OK.
Anyways, I have a Hydrometer probe and keep logging numbers from 5 spots on our bathroom floor, it quite small only 5×5 feet. It has come to 10% in the best spot and 12% in the worst, seems it won’t go under that. We have only been 3 days using the bathroom fan and Kitchen fan to move air, I tried a portable heater but somewhere I read against it and removed it. Mind we live in BC, Canada and it’s already getting cold and damp here… not the best season but here we are…
We also have an underground parking under our slab, and no Idea what kind of water barrier was used, we could not use any in our side because of the electric heat mat. So I wonder if we are actually pulling moisture out of our underground and will never come to the right numbers. Also, we can not isolate the bathroom since its the only one in our apartment and we use it on a regular basis.
Any idea of what the best way would be to deal with this situation?
Sergio:
Thanks for the questions. Unfortunately, I am not familiar with the moisture scale you are referencing. It most definitely isn’t RH% in the substrate as most finish products would specify. You would usually see 75%RH + in those situations. As far as drying, the heat and air movement probably is a good thing. The way to verify is to measure the ambient RH% before heat and then measure it after heat. As long as the heat is “dry” and the moisture in the air isn’t stagnating, then it is probably helping. The other thing to keep in mind is that most self-levelers, especially at a ¼” thickness, are designed to dry very quickly. Many people won’t even measure moisture in the leveler, they measure moisture in the substrate below, prior to the leveler.
Thanks,
Jason
Hi Jason – Thanks for this helpful article.
Here is my basic question: How much moisture should I expect as my concrete basement cures over its first year?
Background: We installed a full concrete basement in April as part of a major renovation/rebuild. The space (pre-concrete) was bone dry (almost zero moisture in the dirt). We have a good sealer/vapor barrier + french drains etc., so don’t believe any water is getting in (plus it hasn’t rained – we’re in California) . . . but the basement was quite damp and some of our things got a bit moldy. I just bought a good de-humidifier and it is pulling about 2 gallons of water out of the space each day. Is this normal? It is a 1400 foot basement with a fairly thick slab and walls, with basically no place for the water to go but to evaporate into the space.
Thanks in advance for your reply.
Kai
Oakland, CA
Kai:
Thanks for the questions. Assuming there is a vapor barrier directly below the slab, keeping ground moisture from penetrating the slab, then all you are dealing with is construction water. A rule of thumb says that once there is constant heat/air/humidity in the ambient space, it will take approximately 30 days for each inch of slab thickness to reach a relative humidity, in the slab, of around 85% to 90%. I hope this help. I hope this helps.
Thanks,
Jason
I poured a slab outside my house and didn’t use any vapor barrier. It’s been 2 months and the slab has a big spot. I dryer using a torch and still shows moisture in the slab. Is there anything gong I can do to remove the dark spot from the slab?
Ramon:
Thanks for the question. There are many times that concrete may have color variations, some of which can be moisture, but other times can be caused by various other inconsistencies in the material. If the inconsistency is that bad, you may think about some kind of topical color coating to make the slab look uniform. Good luck.
So, you’re saying for a 6″ sunken living room floor, it would take 180 days before we can put a new floor in? Is that true everywhere? I know of builders that are done start to finish with houses in 3-4 months. We want to raise a living room floor and have been told it’s better to use concrete than to raise it with wood. Is that right? We can’t wait 6 months!
Jean:
Thanks for the questions. Yes, the information states 30 days for every inch of slab thickness, once the environmental conditions are conducive for drying. So what that means is that in a lot of cases, it takes longer than that. The level of “dryness” is also dependent on the type/breathability of the flooring being used. Wood flooring being glued to a slab is potentially more moisture sensitive than say a breathable carpet. There are also various adhesives and product that minimize the amount of moisture that can escape for the slab, allowing for products to be installed on the slab faster. I would consult your flooring contractor for more in-depth information on acceptable products. Good luck.
Jason
Hi. We have a sunken living room and water issues. During a hurricane water bubbled up from below the wood floors and we had to tear everything out. Engineer came out and told us to fill it in. We used tar around the edges and poured 6 inches of concrete. Two weeks post pour our concrete moisture reading is 19. We are running two dehumidifiers 24/7 but we live in very humid climate. How long do you think it is going to take for floors to dry enough to install engineered wood floors? Do you have recommendations for moisture barrier?
Bethany:
Thanks for the comment. Unfortunately, 19 doesn’t mean anything to me in relationship to industry accepted measuring standards for concrete and flooring materials. What I can tell you though is the rule of thumb in relation to drying of a slab is this: it will take approximately 30 days for every one inch of slab thickness to reach a level close to being dry enough for that wood floor. On the barrier, I don’t recommend products, but I will tell you, in most cases, you get what you pay for. There are some very good wood glues out there that may work fine. Good Luck.
Jason
Jason
We had some water damage, had to rip out our laminate flooring. Measured our moisture level which ended up being 98%. Been running dehumidifiers, ac is down, fans blowing, however after 3 weeks it seems we have gone nowhere. Is there any other options that can help us?
Sander:
Thanks for the question. You don’t say how much moisture or for how long, but it can take a while to naturally dry out a slab after a flooding incident. Depending on the type of flooring, there may be acceptable installation methods for higher RH applications. Contact the flooring manufacturer and see if they have any recommendations.
Thanks,
Jason
I have a slab that won’t dry. Our slab leak presented on May 3rd – we had dehumidifiers, fans and a vapor barrier for 6-7 days before we decided to pull the floors up. Then we tried them on top of the slab for at least another 7-10 days, and nothing changed. Then we had the floors “peeled” of the adhesive layer on top of the slab to “let it breath.”
Now, almost a full month after that, our slab still wont dry. We’ve been running fans on the floor and the ac 24/7 for last 3 weeks. We were told to let air in, cool outside air and ac. We are hesitant to use another vapor barrier and use dehumidifiers and heat again as it could add damage to our newly remodeled downstairs.
Now, we want to drill 2 16″ holes in our slab to see what is causing these two spots to remain. Mind you, that our entire water system under the slab has been cut off and our house has been repiiped. Yet, our slab won’t dry. What should we do?
Kevin:
If I am understanding, correctly, what you are presenting, you had a plumbing issue BELOW the slab and the moisture made its way INTO the slab and up to the surface, affecting the finished floor? Based on this, it would be a pretty safe bet to assume that you don’t have an intact vapor retarder below the slab. With that, you could apply some type of GOOD quality vapor retarder on top of the slab, expediting your ability to reinstall the floor and, also, mitigating against potentials like this in the future. Keep in mind, not all vapor retarders are equal and if the claims seem too good to be true, they probably are. One thing you never state is how high the moisture levels are within the slab. It is critical to know this so you know how to remedy it.
Jason