Engineered Flooring Installation on Concrete
Don’t let the “engineered” give you the wrong impression. Engineered wood is real wood. Although it’s not made of solid hardwood, it doesn’t mean that engineered flooring does not provide all of the warmth, longevity, and elegance of a hardwood floor.
Engineered wood flooring is chosen for quite a few locations where you would not expect to see wood flooring due to the strength of its construction, offering additional resiliency against temperature and humidity changes. Built with various types of “core” material, engineered flooring provides a wide range of aesthetic benefits as well with the ability to choose from a wide variety of colors, textures, and wood species for the surface layer. Once installed, engineered wood planks look the same as solid wood planks. Installing Engineered wood flooring is a great project for the DIYer who desires the look of a professional wood floor with the strength and longevity offered by its sturdy design.
Some engineered wood flooring products are designed for glue-down applications when installing flooring over concrete slabs. Other products are better-suited for a nail-down installation where they are secured to a wood subfloor with nails or staples. And for do-it-yourselfers, the preferred method is the floating floor installation which uses no glue or nails. Instead, the engineered wood planks are joined together with interlocking joints, creating a single, continuous layer that “floats” over the subfloor.
This article, however, focuses only on the glue-down application. Nail-down installations are covered in this article.
Acclimate Engineered Flooring
Regardless of whether or not the flooring is glued, nailed, or floated, engineered wood flooring needs to be acclimated to its environment before installation – just like solid wood flooring. It’s important to follow the manufacturers’ guidelines for the proper acclimation procedure and timeline as these may differ from one engineered flooring brand to the next.
Get yourself an accurate wood moisture meter and use it to ensure the wood planks have properly acclimated according to manufacturer’s specifications and have achieved equilibrium moisture content (EMC) with the surrounding ambient conditions. This can be done by periodically measuring the moisture content of the wood until it meets the guideline specs for installation.
There are two types of wood moisture meters available; pin meters and pinless meters. The latter being chosen more often for their non-destructive electromagnetic measurement capability.
Concrete Moisture Measurement Is Critical
Another thing to check is the moisture levels within the concrete slab. Excessive moisture in a slab can damage an engineered wood floor and cause the plies to separate. Most flooring manufacturers require moisture tests for concrete moisture to validate their warranty requirements.
Remember this:
- Every concrete slab has moisture and will always have moisture. What you want is a slab with an acceptable level of moisture for the flooring finish you’re installing.
- Besides the moisture already in the concrete, additional moisture can enter a slab from rainwater, poor plumbing or drainage below or at the sides of the slab, and even humidity in the air.
- To find out if your concrete floor meets the dryness criteria set by your flooring manufacturers guidelines, remember this mnemonic: “If you wanna know, go below.” Scientific testing has determined that measuring moisture conditions within a concrete slab yields more valuable data than only measuring the moisture evaporation emission rate (MVER) at the surface[BM1] [LL2] [LL3] of the slab. To measure the moisture inside the concrete, you will want to conduct a test known as the ASTM F2170 in-situ relative humidity (RH) test.
The RH test uses sensors or probes to measure the RH at a specific depth within the concrete – 40% of the slab’s thickness for a slab drying from one side, or 20% for a slab drying from two sides.
Scientific research from leading academic and industrial institutions confirms the reliability and accuracy of the ASTM F2170 RH test at these depths. The readings will most accurately predict the slab’s point of equilibrium, and therefore the true moisture condition that will exist after the flooring installation.
How to Install Glue-Down Engineered Wood Flooring on Concrete
Slab Preparation
Slab preparation is critical for glue-down and includes sanding, scraping, leveling, and filling low spots because the slab must be flat so the planks can fit correctly.
When “leveling” (actually flattening) a slab, don’t allow more than 3/16” difference in height within a 10-foot radius or 1/8” within a 6-foot radius.
Wood Floor Adhesives for Concrete
Before applying adhesives, you must fill in any voids or deflections in the slab with a cementitious patch or a self-leveling underlayment. An adhesive is not intended to fill voids or deflections.
Use adhesives specially formulated for wood flooring so they conform to the natural characteristics of wood – expanding and contracting. That is, their elasticity ensures that the engineered wood has an ample amount of space to expand and contract without causing the glue to crack or separate.
Be advised: using the wrong adhesive or applying incorrect amounts can lead to a failed flooring installation.
For example, use a wood floor adhesive that contains no water — like a moisture cure urethane or modified silane adhesive. These products are a good choice for these installations because they increase the strength of the bonding agent and offer a degree of structural flexibility.
A glue-down installation requires premium wood adhesives be properly troweled over the concrete slab and the engineered wood planks laid onto the adhesive and locked together at their tongue and groove joints.
NOTE: Wood adhesives recommended today are much more environmentally friendly than in the past, but they cost more. They also require considerably more time to trowel, which adds to the overall labor costs. For more information, visit
http://www.referwork.com/costs/install_engineered_wood_floor.htm.
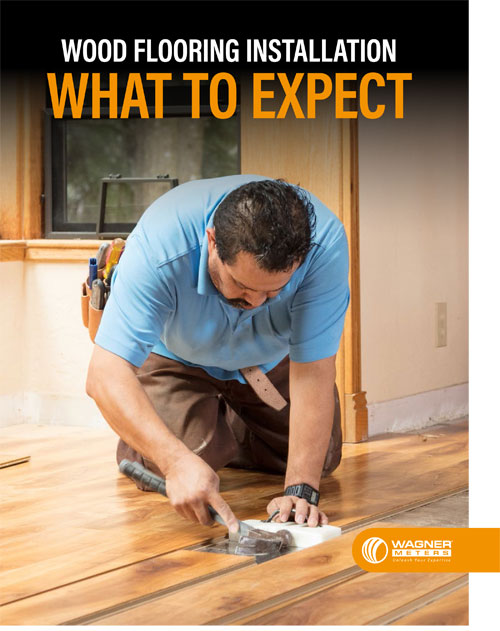
Free Download – Wood Flooring Installation: What To Expect
Previously published by Hardwood Floors Magazine
Installation
Expansion gaps should be left between the flooring and wall. The manufacturer should have recommendations for how wide the expansion gaps need to be. Installing engineered hardwood flooring over concrete too tight against a stationary object will not allow room for normal expansion, and may cause a failure.
The adhesive manufacturer should have instructions regarding specific trowel requirements. Use a notched trowel to spread the adhesive. Pass the trowel through the glue at a 45-degree angle and install engineered flooring immediately after the adhesive is spread.
Important: Only spread the adhesive over small areas ahead of you at any given time. You don’t want the adhesive drying before you can get to that area. If you’re using a urethane adhesive, this advice is even more vital since the adhesive is moisture-cured and sets up fairly quickly.
Lay the flooring into the adhesive with the tongue side of the board facing the center of the room. The hardwood may slip and move at first, so be sure to secure one row entirely before moving on to other rows. The initial row will limit the movement of subsequent rows.
Occasionally lift a piece of flooring to make sure there’s a 100% adhesive transfer, necessary especially for adhesives that have moisture mitigating characteristics. If the board is not entirely covered, remove dried adhesive and apply more.
Be sure to follow the manufacturer’s instructions after installing engineered flooring over concrete. For instance, you might be required to roll and cross the floor with a 100-150 lb. roller after installation to ensure proper adhesive transfer.
Traffic should also be restricted for up to 24 hours after completing the installation to allow drying.
If you are still debating whether to install your engineered wood flooring using the glue-down method, consider these points:
Pros:
- Floor has a solid feel
- Less chance of squeaking or “clicking” due to boards coming into contact with the subfloor with every step
- Permanent installation
- Enables use of flush mount moldings to create dynamic height transitions and allow expansion space
Cons:
- May require rigorous subfloor moisture prep
- Labor costs are higher, typically $3-5 per square foot
- Adhesives can add up to $1.00 per square foot
How to Install Nail-Down Engineered Wood Flooring
Previously published by Hardwood Floors Magazine
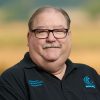
Tony Morgan is a senior technician for Wagner Meters, where he serves on a team for product testing, development, and also customer service and training for moisture measurement products. Along with 19 years field experience for a number of electronics companies, Tony holds a B.A. in Management and his AAS in Electronics Technology.
Related Posts via Taxonomies
Last updated on July 30th, 2021
Tony, I’m not sure the question I submitted this morning posted so I am posting again.
My home is almost 5 years home and is built on a concrete slab. The engineered hardwood flooring (glued down) was damaged and had to be replace. I waited 4 months for the flooring to come in and was told that the mill had a bad run and almost couldn’t fill my order. The old floor was removed and the new floor laid in June so it has only been about 6 weeks since they finished. They glued the new flooring down and when they did they used a strap that they put on the outer edges and the ratcheted together to really pull the boards in. Now I have several boards that are splitting (checking) and some that are lifting up so you can hear the air whoosh out when you walk on them. The humidity in the house is within normal range. My question is this, is it a normal installation practice to use strapping and ratchet the boards together? I am not sure if my problem is bad product or bad installation. Any insight you can provide would be helpful.
Hi Jan,
This would need to be a flooring manufacturers call as to whether it is appropriate for your product. You can use the NWFA inspector website to find a certified inspector: https://www.woodfloors.org/certified-inspector.aspx
Hope this helps.
Tony, my home is only 5 years old and I had to replace my engineered hardwood flooring (it was glued down) because of some damage. The new flooring has only been down since the middle of June. When they installed the new flooring they glued it down and then used strapping and ratcheted it together to make it tight. Now I have several boards that are splitting, some of the boards are lifting and when I walk on it I hear the air whoosh out. Is the use of strapping normal during the installation process. My old flooring didn’t have any split boards (checking) which I understand is caused by expansion. I had to wait over 4 months for the flooring and almost had to wait another 2 months because the manufacturer had a bad run. How do I know if it is bad product or bad installation?
Tony –
Do you have a suggestion for how to transition from 3/4″ engineered wood flooring to bare concrete in areas like utility rooms that have no flooring material on them?
Thank you!
Terry:
Thanks for the question. If you go on google and look for “3/4″ hardwood flooring reducer” you will see a lot of options.
Good luck.
I plan to install an epoxy coating over concrete interior floors. The installer will level and glue down solid wood 4″ wide planks. I’m wondering if gluing over epoxy is a good idea. Any thoughts?
Glenn:
Thanks for the question. I am going to assume that the epoxy is being applied due to a higher than normal level of moisture in the concrete. That being the case, epoxy moisture mitigation products are the gold standard, so as long as proper installation/floor prep is done, I see no issue.
Hi Toney, what type of glue should i be using on a concrete floor when installing engineer wood, also what type of moisture or sealant should i be using. i have about 2300 sqft. to install. thanks
Azad:
Thanks for the question. I wish it was a simple answer. First, I would want to know what the relative humidity test results showed in the concrete. From there, I would consult the manufacturer of my choice for adhesives. Sika, Mapei, Divergent, Bostik, etc. There are many. They can then help you come up with the total solution you are looking for on this project. Good luck.