Calcium Chloride’s (MVER) Achilles Heel
Technical evolution has influenced two guidelines practiced by the American Society for Testing and Materials (ASTM). Specifically, ASTM F2170 co-exists with ASTM F1869 as construction moves from one era of moisture content measurement to another.
Moisture Vapor Emissions Rate (MVER) Regulation:
ASTM F1869: Use this test method to obtain a quantitative value indicating the rate of moisture vapor emission from the surface of a concrete floor and whether or not that floor is acceptable to receive resilient floor covering. The MVER only reflects the condition of the concrete floor at the time of the test.
The calcium chloride (MVER) test has been construction’s traditional choice since the 1950s. Its central tenet is that moisture content can be effectively measured by the rate of moisture vapor emissions. Assessors place a specific weight of anhydrous calcium chloride crystals in a dish which is sealed to a concrete surface for 60 to 72 hours. The weight differential before and after testing reveals the amount of moisture vapor absorbed by the calcium chloride crystals; the rate is indicated in pounds (of water) per 1000 square feet for every 24 hours of drying time. If MVER is below “3,” the concrete is deemed suitable for flooring application.
A pound reading of calcium chloride does not necessarily indicate the total concrete dryness. MVER focuses on weight gain of crystals based on water vapors that rise to the surface area during a timed test. In fact, moisture vapor is a continuous migratory process that is influenced by relative humidity (RH) conditions. An MVER test may reflect moisture content in the top three-quarters-inch of the slab but critics suggest the MVER test does not address moisture content deeper inside the concrete.
Moisture Content Regulation:
ASTM F2170: Moisture permeating from concrete floor slabs affects the performance of flooring systems such as resilient and textile floor coverings and coatings. Manufacturers of such systems generally require moisture testing to be performed before installation on concrete. Internal RH testing is one such method.
RH testing assesses RH at varying depths and locations in a concrete slab. The differences in RH readings indicate the slab’s natural process of moisture migration. Water vapors rise from the bottom to the top in order to evaporate. However, high RH causes concrete to absorb moisture vapor, which slows down evaporation. Conversely, low RH causes concrete moisture vapor to evaporate more quickly.
Wagner Meters’ RH test method quickly and accurately assesses total internal RH – where stubborn vapors are known to hide. Left untraced, residual moisture vapor can destroy the adhesive bond of prematurely-installed floor coverings. They can also lead to costly and perpetual moisture content problems in the slab itself. Luckily, RH testing empowers contractors to preempt these issues by testing RH levels long before they install a floor covering.
RH or calcium chloride (MVER)? Your choice determines the efficiency and quality of concrete installation.
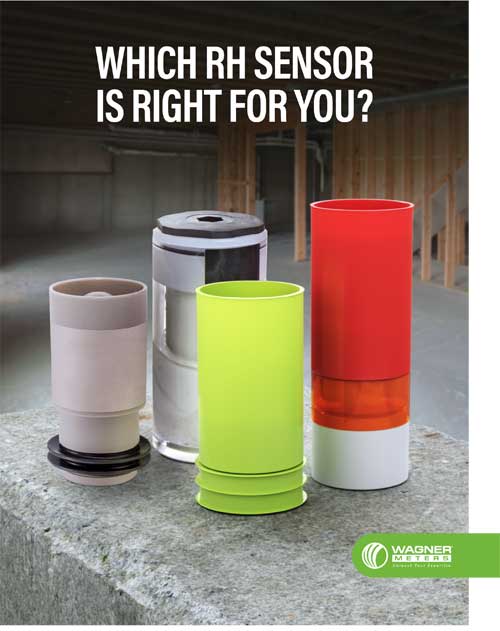
Free Download – Which Rapid RH Sensor is Right For You?
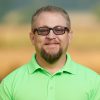
Jason has 20+ years’ experience in sales and sales management in a spectrum of industries and has successfully launched a variety of products to the market, including the original Rapid RH® concrete moisture tests. He currently works with Wagner Meters as our Rapid RH® product sales manager.
Related Posts via Taxonomies
Last updated on September 21st, 2021
HI Jason. I just discovered this site with all of your articles. I’m in awe of your knowledge. Thanks so much. I hope you don’t mind a question.
My basement is about 20×30 ft. It’s got an old slab, maybe 3″ thick. Five years ago I decided to deal with the moisture, which was only a problem here and there, and never pools of water. So I prepped the surface, added an epoxy-based sealer (red color; I forget the brand), primer, then about an inch of self-leveling cement (Custom Building Products) with some pea gravel.
One quarter of the basement didn’t get the red sealer, and will now show some darkness if something lays on it for a few days.
I’d like to put vinyl plank flooring on the basement floor, and am worried that the quarter without the epoxy under the self-leveling will trap moisture.
So:
1. Do you think it’s possible that the moisture is actually really low in that area, and that I might safely cover it with the vinyl floor? Maybe I’m being too careful?
2. Do you know of a different kind of breathable floor covering that I could use in that area?
Sorry to be longwinded. Thanks very much for your time.
Jeff
Jeff:
Thanks for the question. The first thing you should do is call Custom and find out how their leveling product will deal with high moisture and what would they suggest given you already have their product installed. The typical process for something like this would be to test the concrete before anything is installed, determine if there is a moisture issue and if there is install some type of moisture mitigation product on the surface of the concrete. (I am going to guess the red product you partially installed was Red Guard and it is a waterproofing product, not a vapor proofing product) Once this is done, the leveler is installed and flooring. Done out of order, say install the moisture mitigation product on top of the leveler and if the leveler isn’t designed for high moisture it may degrade. Calling Custom may gain you some additional options. From a breathability standpoint, carpet is usually the best. Good luck.