How to Overcome a Wet Concrete Slab
Jason Spangler, the Flooring Divison Sales Manager for Wagner Meters, discusses the two main ways to deal with a concrete slab that is too wet to install flooring.
The First Step to Conquering Wet Slabs: Knowing How Concrete Dries
As with many things in life, the truth lies in the fundamentals. Concrete moisture refers to the composite of four moisture quantities:
- The total amount of water used to produce a concrete batch
- Curing water
- Any environmental water (rain, etc.)
- The water which is bound in the hydration process
When it comes to installing a finished flooring system to the slab, a large portion of this moisture has to evaporate from the slab before a successful installation can occur.
This industry rule-of-thumb applies to every slab: It will take approximately 30 days of drying time for each inch of concrete thickness.
Flooring professionals are encouraged to install moisture tests earlier and monitor in order to ensure the concrete is actually drying “according to plan.”
It is extremely important to get an accurate assessment of the moisture condition because a number of different things can affect how fast the slab dries. Time is not the only factor in the drying equation.
Ambient relative humidity (RH), for example, exerts a significant influence on a slab’s moisture condition. When ambient RH (the water vapor in the surrounding air) increases, the rate of drying slows due to slab moisture retention. When ambient RH decreases, the rate of drying increases as moisture evaporates more quickly from the surface of the slab.
Historically, surface-based test methods were used to try to assess the moisture condition and slab readiness, at the dawn of the 21st Century, industry professionals researched slab moisture assessment in order to improve concrete drying time estimation.
It was methodically determined: RH testing was the most precise and thorough means of MC assessment. Learn more about how to use technology to more accurately predict concrete drying times. One way to quickly find moisture spots in the concrete is to use a C555 concrete moisture meter.
The SCA Recommends Planning Dry Time with RH
The Swedish Concrete Association (SCA) has developed a way to estimate minimum concrete slab drying times at the planning stage, rather than fretting over the poured slab itself while project times swell.
The calculation for “standard drying time” requires several important environmental assumptions, including:
- 7.2-inch thick (180 mm) slab of Portland cement concrete
- Drying temperature: 64° Fahrenheit (F); 18° Celsius (C)
- 60% ambient (air) RH
- Elevated dual-side drying
- Curing conditions: two weeks of rain and two weeks of high RH (prior to commencing drying)
- Estimation parameter: water-to-cement ratio
- RH which characterizes moisture conditions after drying: 85% and 95%
From this “standard drying time,” they have also estimated certain correction factors that can be used for additional variables, such as varying slab thickness, slabs only drying from one side, varying W/C ratios, etc.
Although the estimation method above is not scientifically corroborated at this time, results of testing did provide an informative variance of slab drying time estimations – enough to have drawn recognition from the Portland Cement Association (PCA). At the very least, the Swedish way proves to be a cautious advancement in “rule of thumb” calculations.
The American Society for Testing and Materials (ASTM) also established the standard ASTM F2170, which recognizes using RH as a methodically-sound way to assess slab moisture conditions.
When Natural Isn’t Fast Enough
Ideally, allowing concrete to dry naturally is usually best. But construction project schedules often don’t allow enough time for this critical process.
Below are some steps installers can consider when a concrete slab contains excess moisture:
- Ventilation increases airflow across the concrete surface to help carry away the evaporating moisture. The more airflow going over the slab, the faster the water will evaporate.
- Heating (or drying) also increases the evaporation rate by causing the water to move to the surface more quickly.
- Dehumidification reduces the dew point of the air surrounding the slab so that more of the moisture in the slab can evaporate through its surface. Heating is one form of dehumidification, but two other common approaches are condensation dehumidification and desiccant drying.
- Condensation dehumidifiers use cool air. This drops the dew point so that moisture can be collected and drawn away. NOTE: Most installed HVAC systems are not capable of removing the amount of moisture emitted through the drying process of a concrete slab.
- Desiccant-based dehumidifiers move humid air across a desiccant material that binds and holds the moisture. A hot air stream then releases the moisture from the desiccant and vents it away from the slab. Once moisture is removed from the desiccant, the process is repeated until the concrete reaches an acceptable moisture level.
In addition to ventilation, heating, or dehumidification, installers could also consider the application of moisture mitigation products designed to seal off the slab. Keep in mind that surface preparation is usually required for these types of products, but consult the manufacturer for specifics.
When using adhesives make sure they offer an appropriate moisture tolerance for your flooring project. If not, excess moisture can cause adhesive failures.
Floating floors are often used for floors where high moisture situations occur, but even these types of floors can be ruined by moisture. When a floating floor is used, manufacturers recommend installing a moisture barrier between the subfloor and the floating floor to prevent moisture intrusion. Keep in mind that if the barrier is compromised in any way, moisture can damage the flooring or finish.
How Can My Slab Still Be Wet?
It either takes time or money for concrete to dry appropriately or to be acceptable for a finished flooring product. With that and the compressed schedule that we have today with new construction, usually, time is not an option.
So the only option at that point is money. Money to bring in dehumidification equipment. Money to turn the HVAC on and get it up and running earlier so that you have an environment that’s conducive for the drying of the concrete.
Another option, from a money standpoint, is topical moisture mitigation products. This class of products is applied topically to the concrete and encapsulates the moisture within the slab so that it lessens the impact that the moisture can have on the adhesive layer or the finished floor product.
As with any other products out there, not all of them are created equal. You need to follow strict adherence to the manufacturer’s guidelines.
Keep in mind, older concrete slabs are still at risk. We hear people say all the time that they don’t even bother testing old slabs because “it’s gotta be dry because it’s so old!” Beware. With those older slabs, the potential of there not being a vapor retarder underneath the slab or a vapor retarder that’s not intact anymore is usually fairly high.
So by doing a concrete moisture test you have the ability to identify those potential issues and you can catch them. Some other ways they’ll do things is they’ll do core testing to verify whether or not there is a physical vapor retarder underneath it.
You either need a vapor retarder underneath the slab during the construction process or a vapor retarder on top of the slab being a moisture mitigation product in order to have a successful flooring installation.
Test for Accurate Moisture Condition
No matter which method is used to deal with excess moisture, the only accurate way to assess a slab’s true overall moisture condition is to test below the surface of the slab.
This is best achieved with ASTM F2170 in situ RH testing. Unlike surface-based methods, RH testing accurately measures moisture conditions within the slab by placing probes at a strategic and proven depth.
Moisture typically moves through a slab from the bottom to the surface during the drying process, thus forming a moisture gradient.
Studies at Lund University in Sweden and elsewhere have shown that RH measurements taken at a specific depth provide a reliable indication of the moisture that the flooring will “see” once the slab is sealed. Therefore, RH readings can be compared to a given floor product’s moisture tolerance, as specified by the manufacturer, for a reliable indication of the slab’s readiness.
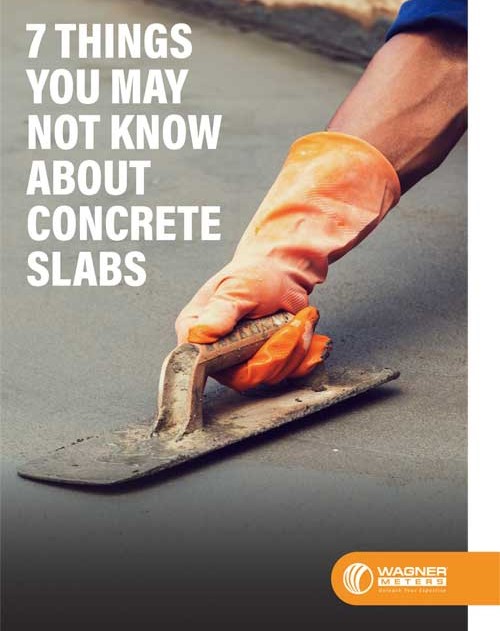
Free Download – 7 Things You May Not Know about Concrete Slabs
Technologically advanced RH test kits are available from various manufacturers. These kits are affordable, simple to use, and provide fast results that conform to ASTM F2170 requirements.
This makes RH testing easy for contractors to perform themselves without relying on an outside testing service. Wagner Meters has introduced an improved version of the popular Rapid RH® in situ concrete slab RH testing system that features greater responsiveness in high RH environments as high as 100%.
The new Rapid RH L6 sensors now provide time-stamped readings that can be retrieved by an upgraded Total Reader® device that connects via Bluetooth® wireless signal to the DataMaster™ L6 smart device app. The app stores, analyzes, and emails reports generated from L6 Smart Sensor data.
To Ensure Success
So when excess concrete moisture threatens to jeopardize a flooring installation, there’s no need to despair. Contractors have many options for satisfactorily addressing the moisture and achieving a successful outcome.
Regardless of which options are used, always be sure to perform an in situ RH test. This helps you to know when a concrete slab is ready for the finished floor and won’t be at risk for moisture-related flooring failure.
Questions or comments? Drop us a line in the comments below or give us a call worldwide toll-free: (541) 291-5123
Are you looking for a concrete calculator to estimate how many cubic feet and cubic yards of concrete you will need to fill your space? Try out our concrete calculator.
Disclaimer: The Swedish Concrete Association method is a guideline only and should not be used as part of any construction document. Actual field concrete installation drying time calculations must be conducted by qualified personnel, based on actual job site conditions. Reference to the method here is for information purposes only.

Wagner Meters is a family-owned American business that aims to provide solutions in moisture measurement technology that will enhance the quality and value of each customer’s project. With an almost 60-year legacy of innovation, Wagner continues to be a resource for both individual craftsmen and high-performance commercial endeavors.
Related Posts via Taxonomies
Last updated on June 1st, 2022
Thanks for this great article. We had a 6” 30×60 slab poured in May 2022 in central Texas. Unfortunately, it was not sealed after it cured. Walls and a roof have been constructed on this slab, and in the seven months since, it has rained multiple times.
There are large framed openings for windows (two 9×6, six 3×6) and an 8’ man door. I know it was a mistake to wait this long to seal the slab.
Here’s my question: should we rent an industrial dehumidifier and a large heater/blower to try to dry the slab now while windows and doors are not sealed? Or wait for the structure to be enclosed and do it then? It’s obvious from looking at the multiple dark patches that the slab is holding moisture. 24×60 will be exposed concrete and the rest will eventually have a glue-down engineered floor.
What would you recommend? Thanks so much.
Lista:
Thanks for the questions. I would get the building enclosed as quickly as possible, get permanent heat into the environment (at least the area that will receive wood), and then do some moisture testing of the slab with either a relative humidity sensor like our Rapid RH L6 or with a calcium chloride test. Once you have these results, compare them to the flooring manufacturers guidelines to see where you stand. Once you have this information then you can make a plan on how to dry things out, if necessary.
Will putting a metal (iron/steel) safe over the top of concrete (fairly fresh) cause the iron/steel to rust?
Hi Jason,
My condo was built in 2017 however the slab was poured in October, 2016. I moved in June, 2017. I have purchased two of the Wagner Rapid RH test kits (L5 & L6). I experienced mold in my new condo and the RH readings were extremely high. I had two industrial dehumidfiers installed and the RH numbers in the sensors have slowly decreased however
the RH in the slab ( garage location) is still 99RH. There is no vapor barrier in the garage. Will this extremely high reading in the garage affect the interior of my condo? What is the normal RH range for the interior for the age of the slab (4.5 years)? Thank you.
Donna
Donna:
Thanks for the question. Constructed properly, I wouldn’t expect the high RH% in the garage to have any real impact in the interior of the house. Very seldom will you see a slab of any age below 75% RH. I hope this helps.
We have a home built in 1994 with a Lanai covered in a tile that appears to be terrazzo. There was indoor outdoor carpet over this for many years with no obvious problem. Recently we had new indoor outdoor carpet put in and after only about a month there is moisture present in the carpet. We are in Fl but have had minimal rain recently. Could this be from the adhesive used to install it? What would be our next move or recourse? Thank you.
Woodrow:
Thanks for the question. There could be a difference in the breathability of the carpet, differences in the air conditions in the Lanai causing condensation, or differences in the adhesive. I would have a discussion with the installer to get their input and remedy. Good luck.
Great article! We work in the concrete biz and are always looking for tips to improve our performance. The little nugget I pulled out of this article is
“It will take approximately 30 days of drying time for each inch of concrete thickness, to achieve a level suitable for most finishes, once the environment is conducive for drying”
Just having a more statistical fact to relay to our customers etc will help them understand the process better. We are in Grand Prairie, TX and are always trying to improve for the environment were in. Thanks for putting out great content!
Best,
Tom
Wet slabs are such a big problem. It cannot be stressed enough. Thanks for all this vital information on the topic. Very useful blog post.
My house was built in 1989. Recently, I was about to have engineered floors installed in my living room and kitchen – literally the day the guys were here to install they did a moisture test on the concrete slab and it came back with 80 in some places and 90 in other. Needless to say, they cancelled the flooring install because the product would fail under such high moisture levels. There is no moisture in the walls and we never had an issue with the existing carpet. Half the house is concrete slab the other portion is a subfloor that is above the basement. We have carpet on the concrete and porcelain tile in the kitchen on the subfloor. Again, never any issues with the carpet lifting on the slab. Should I be concerned? What are my options? I was thinking that we should just go with porcelain tile that looks like wood, but I’m concerned there’s an underlying issue that’s causing the moisture. We have a humidifier in the basement, but it’s so cold right now the humidity levels are very low in the basement and we never had an issue with high humidity upstairs in the living room or kitchen..
HML:
Thanks for the questions. My guess would be that with a breathable flooring product like certain carpets, relatively higher moisture levels in the concrete wouldn’t create an issue. Changing to a non-breathable product though creates certain issues that need to be addressed differently. Notice, I didn’t say the flooring can’t be used, it just may not be able to be installed via the simplest and cost-effective way. My guess is you could find a way to use the wood, but it would require a moisture mitigation product to be installed on the concrete prior to the adhesive and wood. You may also be able to find a more robust adhesive. I would consult more with where you purchased the flooring product or with additional installers.
Thanks,
Jason
Jason,
As always you are a wealth of information. Thanks for being who you are and representing our industry in the professional way you do.
Sincerely
Greg Hathaway