3 Dangers to Avoid When Installing Wood Floors Over Concrete
Installing hardwood (or any kind of wood—engineered, laminate, etc.) floors over concrete might sound easy, but do you know what problems could happen? If you don’t take the necessary steps to avoid these 3 dangers when installing hardwood floors over concrete, you could be headed for trouble.
Yes, new slabs can be tricky, but don’t forget that an old concrete slab can still cause big problems.
If this is news to you, pay close attention to these 3 big dangers.
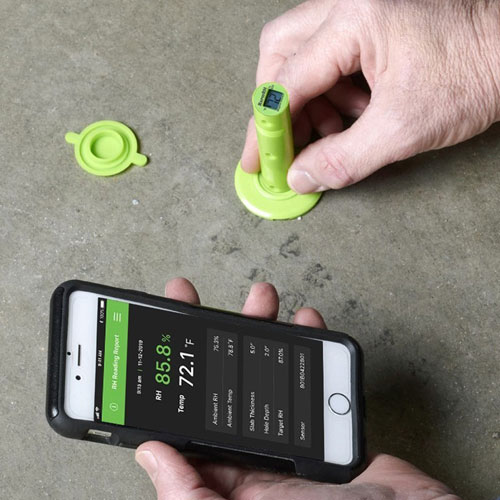
In-situ RH testing provides the most reliable way to identify excess moisture in concrete slabs.
Or if you’ve learned this before, now might be a good time for a refresher.
Avoid these 3 dangers:
# 1 Danger: Not testing with in-situ relative humidity sensors before installation
A new concrete slab is the most likely type to have excess moisture, mainly because a decent amount of water is necessary for the initial creation and placement of concrete. But not all that water is supposed to stay in the slab forever.
Excess water must be allowed to evaporate through the surface before installation.
If not, major moisture issues are inevitable.
Even old concrete slabs, if not installed properly or because of a variety of external moisture sources, can end up with too much moisture in them.
How?
Maybe there’s no vapor barrier. Maybe there is one, but it’s damaged. Maybe there’s a plumbing leak affecting the slab. No matter what the source of the moisture is, it needs to be handled before installing wood floors over concrete.
Best way to identify excess moisture? By testing with in-situ relative humidity (RH) sensors.
These sensors are placed at 40% depth in the concrete, allowed to acclimate for 24 hours, and then scanned for readings of moisture levels. By testing moisture levels in the concrete and not on it, you’ll receive an accurate reading of what the surface of the slab will “see” when the moisture has equilibrated.
#2 Danger: Not acclimating the floor to the installation environment
Before even one hardwood floorboard is laid down, it must have had plenty of time to acclimate to the end environment.
That’s right. It can’t come straight from the source to be installed immediately on the concrete. The wood needs to be placed in an enclosed environment with temperatures and humidity similar to that of the installation environment, if not in the actual installation environment itself.
Since wood is hygroscopic, it will absorb and release moisture until it has reached equilibrium. When it absorbs moisture, it expands. When moisture is released, the wood contracts.
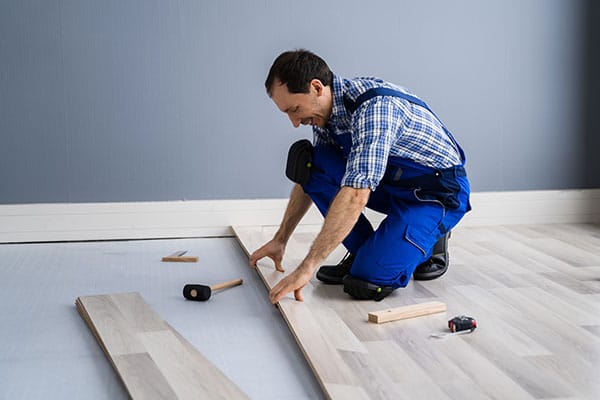
Before installation, be sure the wood flooring has fully acclimated to the indoor environment where it will be used.
If the boards are installed before the wood stops expanding and contracting, it’s likely there will be cracks or swelling in the boards—a huge issue!
Make sure the hardwood flooring has fully acclimated to the environment you’re installing it in to avoid these big headaches.
#3 Danger: Not using an accurate wood moisture meter
A good flooring installation job is only as good as its least accurate wood moisture meter.
What does that say for your job? Doing well? Time to consider upgrading?
An accurate wood moisture meter can save a flooring job from disaster. After all, when you’re installing high-dollar, high-quality wood, you want to make sure your customer is going to be pleased with your work for years to come.
But the fastest way to jeopardize that is by using a less-than-accurate wood moisture meter. The risk just isn’t worth it.
And since you’re working with beautiful flooring you want to stay beautiful, your best bet is to use a non-damaging pinless moisture meter. No more unsightly holes in your boards, and you still get the readings you need.
Talk about a win-win!
What if you don’t test the concrete for moisture?
Then there’s a high chance the wood floor will cup or buckle due to the moisture rising through the concrete and escaping.
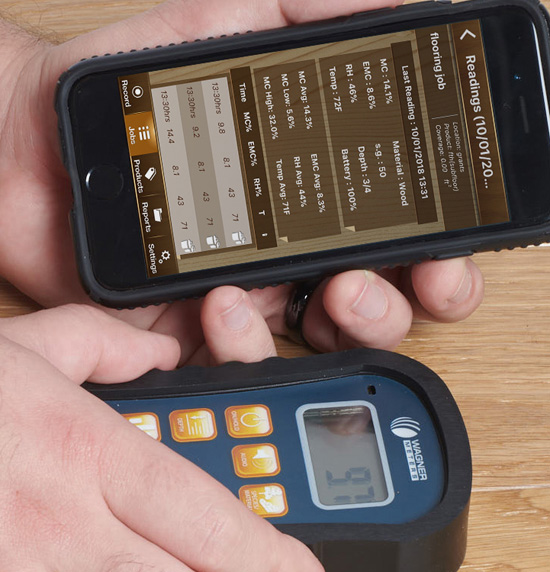
Using an accurate wood moisture meter helps ensure that your wood floor installation will be successful.
This is arguably the most important step to take before installation.
Sometimes it can feel like an easy step to skip because…
…you’ve been in the industry for years.
…you intimately know the concrete you’re working with.
…there hasn’t been any rain.
…the building is enclosed.
…the concrete looks the right color.
But if you can’t look at the slab and immediately know the moisture reading, then skipping this step of testing moisture in the concrete runs the risk of ruining the whole job.
Best practices to avoid dangers in installing hardwood floors over concrete
First, prep your slab. This means clean it up, smooth it out, and—you guessed it—test it.
Then, install an underlayment/subfloor. By giving your hardwood something to actually “grab on to,” you’re giving it the best possible chance of lasting years and years.
Don’t forget to acclimate and test the hardwood flooring. And if the readings are coming back too high, allow additional acclimation time. The extra time is worth it when you don’t have to rip out and replace the wood at some future time.
Finally, lay your flooring, add finishing touches, and enjoy. Then you can have peace of mind that your job will last for the long haul. And who knows, maybe your work was so impressive that your clients referred you to all their friends and family.
Your reputation will precede you, and you’ll have customers for years to come. Isn’t that the dream?
Previously published in Premier Flooring Retailer magazine
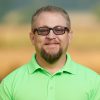
Jason has 20+ years’ experience in sales and sales management in a spectrum of industries and has successfully launched a variety of products to the market, including the original Rapid RH® concrete moisture tests. He currently works with Wagner Meters as our Rapid RH® product sales manager.
Related Posts via Taxonomies
Last updated on March 21st, 2022