Green Lumber or Kiln Dried Lumber: Which Kind Do You Need?
Forestry, done well, is a combination of science and nature which results in strong, durable wood. However, all wood species are harvested in the “green” condition, which is a term for the properties which behold wood in the wild.
There’s Green Wood
Many observers would be shocked at the high (“green”) moisture content (MC) of some wood species. Since trees comprise an autonomous eco-system of water and nutrients, it stands to reason that sapwood (the layer next to the bark) is generally higher in MC than heartwood (inner wood which has died). Sapwood distributes water and nutrition through a tree. The heartwood, or inner wood, becomes infiltrated with gums, resins, and other materials.
This makes it more resistant to moisture flow and thus, the heartwood usually requires longer drying times than sapwood. Sapwood and heartwood will affect the drying curves for each wood species.
A wood’s MC is also a dynamic exchange between the wood itself and the surrounding air. When the relative humidity (RH) in the air rises, wood absorbs moisture from the air; when the RH falls, wood releases moisture into the air. This occurs naturally, and it occurs throughout a wood product’s lifespan even after it has been harvested and kiln-dried for human use. Wood producers, builders, and consumers need not fret over such an organic, natural process, but a thorough knowledge of it will guarantee success with wood in all sorts of product applications.
The key to wood strength and performance over time is to dry the wood appropriately to its optimum MC depending upon the end product’s service conditions and the end product’s installation destination.
There’s Kiln-Dried Wood
Wood in “green” condition must be kiln-dried in order to be used as construction grade lumber for building purposes, as an example. Lumber production is a complex process in which green timber is sawn, dried and processed. The natural air-drying of lumber can be a long process, so oftentimes lumber will be kiln-dried to speed the process along. Kiln-drying is basically a process of placing sawn lumber into kilns where heated air is circulated and the temperature and RH of the kiln is controlled for the purpose of reaching the wood’s equilibrium moisture content (EMC): a balance between the MC of the wood, and the RH of its surrounding environment, depending upon the end wood products application specifications. Once the EMC is achieved, a wood’s MC can vary with slight changes in the RH of the surrounding environment without jeopardizing the strength and structural integrity of the end wood product.
Lumber producers deploy expansive and expensive wood MC control systems at all phases of wood production. Kilns are an integral part of the wood’s MC measurement and management process, as the kiln-drying procedure is where the green lumber is dried to its optimum EMC.
There’s a Moisture Meter to Measure It
A wood moisture meter is crucial in establishing and maintaining healthy wood MC levels at each stage of lumber production. A wood moisture meter is a tool which measures the wood’s MC. As green wood circulates for processing in a mill, in-kiln and in-line MC systems measure and document the wood’s MC and track the efficiency of the kiln-drying process. Professionals carefully monitor and control the process to optimize the harvest. Kiln operators and quality control personnel deploy hand-held wood moisture meter products to conduct as many spot-checks as needed to verify the mill’s kiln-drying efficiency.
Ecology is merging with forestry in the modern era to make MC measurement and control an ongoing matter of wood maintenance. Wagner Meters, a family-run industry leader in MC measurement technology, has developed several wood moisture meter products to assist industry specialists, retailers, wood flooring installers and owners and hobbyists in protecting their investments.
As the world awakens to its own nature, wood moisture meter technology has advanced greatly. Wagner Meters features pocket size digital and analog styles of its wood moisture meter products. Now there’s a cost-effective, reliable wood moisture meter to suit any wood measurement application goal, from the home to the lumber producing mills.
To learn more call: 800-634-9961.
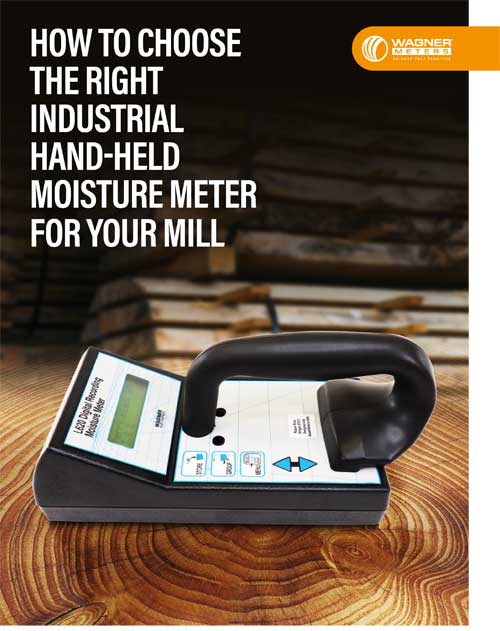
Free Download – How to Choose the Right Industrial Hand-held Moisture Meter for Your Mill
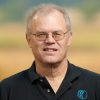
Larry Loffer is a senior technician at Wagner Meters, where he has over 30 years of experience in wood moisture measurement. With a degree in Computer Systems, Larry is involved in both hardware and software development of wood moisture measurement solutions.
Related Posts via Taxonomies
Last updated on June 8th, 2021
I just read your article about green lumber and kiln dried lumber. I learned a lot from it! Thanks for writing this post because it has helped me figure out how to budget my projects better! I’m now more informed on the kind of wood to use. Thanks so much for sharing this knowledge with us!
It’s clear to see that many people have a lot of misconceptions about the two types of lumber, and we’re glad you’re looking to clear things up for them.
Thanks for the information. I’ll be sure to share it with our team!
Hi Larry, the Amish built sheds in our area use rough cut lumber. Is there any disadvantage to this as a buyer? Do they come with any potential problems? Any information would be appreciated
Dom
Hi Dominic,
Structurally, rough-cut lumber is as good as planed lumber as long as the lumber was dried properly. For an outdoor shed, the moisture content isn’t as critical. You might see warps, twists, etc if the lumber wasn’t dried prior to building the sheds. Rough cut lumber can be difficult to paint and/or stain.
This topic always gets a mixed response within the log cabin industry, depending on who you speak to. There is much debate surrounding which logs to use to build a log cabin, from the species of tree that you choose, to whether you should use dead standing or green logs, kiln or air-dried logs. Freshly cut trees have high moisture content, and if they are used to build a log cabin immediately, the logs will have a tendency to warp, shrink and twist causing the log cabin to be less structurally sound. That’s why most people choose to dry their logs out before building a log cabin, which allows them time to stabilize, there are a few different methods of doing this; kiln drying them, air drying them. The other option is just to use the dead standing as soon as they’ve been harvested. Some professional builders argue that air drying logs is the best option whereas other are adamant that kiln dried logs are more stable. If logs are air dried correctly, and for the right length of time, they will reach the same equilibrium moisture content as kiln dried longs. While there are plenty of reasons for and against each method, it really does fall down to which method you prefer, your timeframes and budget.
In 1978 I built my own home and contracted out some work. I hired framers to dry-in the house. When talking to them they told me I could save money by using green lumber. And yes there was a big difference in price. I ordered the lumber and it was delivered, but then the framers were delayed about 3 weeks which left this green lumber bundled at the job site. When they unpacked it all the inner wood had turned green or black. They said that is normal and built the house. So my lumber is black now!!! When inspectors come they always note a moisture problem in my crawl space, which I don’t have, so I take them to the attic and show them the roof rafters.
Oh well, my observation was a few boards warped and I fixed them buy cutting and putting a long splint on each side. No problem in 40 years.
But I always thought the green lumber had more structural strength which is contrary to information I’m reading now. My observation is that my green lumber is much harder than kiln dried lumber I get now. My old green lumber is so hard it is difficult to drive a nail in it without bending it. I only use screws now! I also noted that the green wood I removed for renovations over the years is much harder to saw.
Could you help me understand why articles do not mention how hard green lumber gets? And does this hardness make it stronger? And why is my green lumber so hard?
Charles,
Air-dried lumber is more stable than kiln-dried lumber because it’s not forced dried through high temperatures, but rather a natural slower process. As the timber air dries the cells collapse, slowly causing them to compress and stay put, so when air-dried lumber absorbs moisture, it doesn’t swell as much hence it becomes more stable.
Kiln-dried is a forced but controlled process where humidity and temperature are controlled using steam and fans for drying, because of its fast drying due to high temperatures, the cells collapse quickly rather than slowly as it would with air drying.
Thanks.
Is it possible with the Dual Depth feature of the newer moisture meters to detect Case Hardened lumber?
Hi Paul,
I would like you to contact our application expert, Ron Smith here at the Wagner office regarding this question. His phone number is 800 634-9961 ext 225 and email is rsmith@wagnermeters.com.
Hello Larry,
I have to fix a floor joist that in the basement supporting the first floor. The joist is 13 feet supported at both ends. The rot extends about 4 feet from one end. Because I cannot get a 2x8x13 board into my basement and put it in place, I will be trying a 12 foot length and possibly a 10 foot length and sistering it to the existing joist, which is in good shape other than the last 4 feet, and supporting just one end of the new joist, shimming as necessary.
The existing joist is 2×8 Fir and is slightly larger than the modern green boards. My question to you is should I use a green board or either a kiln-dried or air-dried board to avoid crowning and shrinkage as the new board dries? My local lumber yard tells me that dried lumber has to be special ordered and could take up to 3 weeks to obtain.
Thanks for any help you can extend.
Chris, It’s always safer to use kiln dried lumber. Green lumber can shrink and/or twist as it dries.
I’ve noticed a yellow pine sawmill nearby is kiln drying lumber for only a few hours. The lumber is continually fed through the kiln with lumber sticking out both ends and the doors never closed. They don’t put slats between the boards to provide air circulation either. Their bundles are about 25 ft by 25 ft. I don’t see how the lumber could be properly dried in this manner. Also, after kilning the lumber is left outside in the rain, Example: A tropical storm recently passed through. We got a lot of rain. Some railroad cars loaded with lumber got very wet. Just before shipping, the white plastic covers were placed over the lumber. Does this make sense? Are they properly kilning the lumber?
Hi Steve,
Sounds like your neighbor has what’s called a “Continuous Kiln”. These are fairly new and the science behind them supports more even drying along with energy savings.
They typically will insert “stickers” between each layer for optimal air circulation.
Perhaps their goal for this batch was not to dry the lumber. Sometimes mills will heat the wood enough just to kill insects.
Or, maybe this batch was sold as green (Not kiln dried).
I share your concern if they sell this as kiln dried lumber.
I’m looking into building my home through the process of milling my own lumber. What is the best way to allow wood to dry after milling in order og get building. What’s the timeline on allowing wood to dry and what’s the easiest method in doing so?
Hi Jack,
The easiest and cheapest way to dry your own lumber is to place “stickers” or spacers between the boards to allow air to reach each board. This is called ‘Air Drying”. Make sure the stickers are right underneath each other.
The disadvantage is that it can take weeks to dry depending on the surrounding conditions.
Another option is to ‘Kiln Dry’ your lumber. This involves placing the lumber in a kiln where heat is applied. This method only requires a few days to dry.
Here is a good link to air drying:
https://www.popularwoodworking.com/air-drying-lumber/
Here is a couple good sources for building your own kiln:
https://dnr.wi.gov/topic/forestbusinesses/kiln.html
https://woodmizer.com/us/Products/Secondary-Processing/Kilns?keyword=&creative=244273281984&gclid=EAIaIQobChMIpv6BmfGh3QIVAWl-Ch027QFtEAAYASAAEgJml_D_BwE
Whichever method you choose, a good moisture meter is essential.
I recommend either the Wagner MMC210 or the L620.
Here is a link to both with more information:
https://www.wagnermeters.com/shop/mmc210-digital-proline-moisture-meter/
https://www.wagnermeters.com/shop/l620-lumber-moisture-meter/
Thank you
I live in New Orleans area. A contractor installed tongue and groove kiln dried wood on my front and back porches. He then used an oil base primer and 2 coats of Sherwin Williams industrial enamel. Within 6 weeks the paint started peeling and sometimes the primer came up, too. It has even peeled in areas outside of the railings where only rain and sunshine touch it. The paint seems to shrink wrap the wood after a few weeks then start peeling.
Contractor just wanted to touch up paint but every day there is a new little section peeling. I went to Sherwin Williams who said they do not recommend primer on wood floors for their industrial enamel. They say paint and primer should be removed and then repaint the porch. They have offered to supply more of the same paint. Contractor doesn’t want to sand and is saying that kiln dried wood must be primed according to a warranty.
I’m being told that would must have primer and the paint must not have the primer. At this point I think I’d rather have the floors sanded and put water proofing stain. Any suggestions would be greatly appreciated. Thank you!
Listen to the paint experts. There may be a problem with the enamel bonding to the primer in this case. Staining the porch might also be a good choice. But either way, it looks as though the job will have to be re-started from scratch, with the surface needing to be sanded down.
Thank you so much!!!!!
Hey there
I’m wondering, if when Pine is kiln dried, all of the oils are removed from it? Is there a 100% effective way that pine can be kiln-dried? It is important for my use, as I have animals in which the natural oils in pine are toxic to. I have been told that kiln dried renders it safe, but can’t find any real information about if this is true.
Hi Denee,
Kiln drying removes pests such as pine beetles and other insect infestations. Not all oils are removed during the kiln drying process. I’m not sure what animals you have and I assume you wish to purchase some kind of mulch or wood chips/sawdust. It is best to read the label on the package to see if it is safe for pets and animals. Here is a good article for more information:
https://www.gardeningknowhow.com/garden-how-to/mulch/keeping-mulch-safe-for-pets.htm
Thank you
Hi,
I am exporting teak woods from africa to india for my own sawmill ,
Now indian goverment asking methyl promide certificate or KILN dried , but in African country’s banned methyl promide since 2002. Or the alternative solution is KLIN drier . This kind of KILN drier where can I get this machine .and what the cost ?
Shankarlal,
There are small kilns you can purchase. Here are a couple links:
https://woodmizer.com/us/Products/Secondary-Processing/Kilns?keyword=&creative=244287460511&gclid=EAIaIQobChMIre_Mjouh2QIVFJd-Ch38Ewk-EAAYASAAEgIAt_D_BwE
http://dnr.wi.gov/files/pdf/pubs/fr/FR0396.pdf
Processing firewood from all species of wood. How can we stop the development of mold after we shrink-wrap the firewood and prepare to ship?
Dennis,
Obviously, completely air drying, or “Seasoning” the wood before it is wrapped will prevent mold…. And reduce the shipping weight.
If drying before wrapping is not possible then there are spray products on the market that are “Mold Inhibitors” that you can spray the wood with before wrapping.
Another possibility is to not wrap the wood airtight. Allowing it to “breath” will reduce mold. Perhaps use a strong perforated wrap?
Hope this helps.
Could you use fresh sawn “green” oak wood just weeks after its cut to build a piece of furniture, such as a table?
JB,
Typical moisture contents for making hardwood furniture is 6% to 9%. Your oak can be worked into furniture if it had enough time to dry to that moisture content.
Thank you,
Larry
Hi, I wanted to get some studs but they are klin dried, so I’m a bit worried
the process only uses heat? no chemicals whatsoever? I wanted them to build a part of my lizard terrarium, so no chemicals
Yuri,
Kiln drying itself in the United States does not use chemicals. I don’t know about other countries. Some lumber mills “Pressure Treat” wood after kiln drying to withstand harsher environments better. It would be safer to use “Green” or non-kiln dried wood with animals.
How would I kiln dry driftwood
Hi Kenny,
Fresh sawn wood drying in a kiln is a much different animal than driftwood that has been soaking in salt water. Kiln schedules will vary depending on the species and the amount of time in the water. There may be different species from piece to piece. Moisture detection equipment will be influenced by the salt content.
You may want to post your question on http://www.kilndrying.org; it has experts from various fields that can provide more detail.