High Grade, Kiln-Dried Lumber Isn’t Easy, but Battle Lumber Does It Every Time
The volatility of lumber prices over that past couple of years drives home once more why maximizing lumber yield is a key goal of every sawmill. There have been price spikes due to bad weather negatively impacting access and inventories that have given way to a rough price correction.
Maximizing yield protects sawmills when prices go low and helps them to have inventory to sell when the industry’s inventory levels are low. Battle Lumber Company has been winning its campaign to maximize yield in a responsible, sustainable way since its founding in 1962.
The Wadley, Georgia-based mill has followed a strategy of continuously modernizing its operations and technology to grow into one of the largest mills in the country. Battle Lumber produces over 90 million board feet (BF) each year from its grade mill division. It achieves its consistent production of high-quality lumber by employing advanced technologies throughout its operations, from its high-tech grade mill division to its state-of-the-art dry kilns and sorter with advanced moisture detection system.
Kiln Dried Lumber Supports Grade Mill Operations
Battle Lumber opened its Dry Kiln Division in 1993, with its Grade Mill Division following shortly after that in 1994. The combination of both divisions and the cutting-edge technologies they use has propelled Battle Lumber into its position as a major producer and exporter of kiln-dried lumber. Today, the grade mill produces 90 million BF every year.
Battle Lumber ships out 5 million BF of kiln-dried lumber every month to more than 20 countries around the world. The mill uses its 17 steam-heated package kilns complete with accurate temperature control, to produce continuously high-quality lumber with on-target moisture content levels. With a 100-bay sorter, Battle Lumber efficiently manages a wide array of widths and colors.
Being able to produce a variety of high-volume of kiln-dried grade lumber consistently positions Battle Lumber to prosper even during this period of price correction. Overall lumber production is expected to grow into 2020. Yet forecasted poor weather in the northwest United States and industry challenges in Canada means production growth won’t be consistent across regions.
Omega Moisture Measurement Is Essential Cog in its Kiln Operations
Battle Lumber has recently upgraded its kiln drying operations once more when it transitioned from Wagner Meters’ Apex In-Line Moisture Measurement System to its advanced Omega In-Line System. Both the Apex and Omega systems reliably detect moisture and provide accurate wood moisture measure readings. However, the more robust Omega system handles the volume Battle Lumber produces with the dependable power and speed required.
Dry Kiln Division Supervisor Clay Grace says, “With the Omega In-Line System, we can check each board that comes into the sorter to ensure specified parameters are met since it keeps a tally of each board’s moisture content. If there’s a moisture spike somewhere in the kiln, it gives us a red flag. We can then check the line with hand-held meters to see if it’s just a wet pocket or a problem with the fan, a leak, or something else. In some cases, it may be necessary to re-dry the lumber.”
To meet the demanded variety from its buyers, it’s essential that Battle Lumber’s moisture measurement system can have the moisture content range that qualifies as out-of-spec easily adjusted for different species. Optimal moisture content ranges from the low end with red oak and poplar to nearly double the moisture content for high-demand species like pine and cypress. A major lumber producer needs a moisture measurement system that can detect and react to them all at the appropriate times.
Battle Lumber maximizes the speed of its moisture measurement process by configuring the Omega system to run boards sideways. The Omega’s sideway sensors scan lumber taking more than 300 measurements per second. The speed and volume of data points collected give Grace and his team a detailed profile of each board run through the Omega.

Free Download – How to Choose a Moisture Measurement System for Your Sawmill Buying Guide
According to Grace, “We use the sideways configuration with four sensors because it’s easier to mount and easier to use because of our trimming system. It gives us an average percentage of the whole board all the way up to 16 feet.”
The sawmill has integrated the data generated by the Omega moisture system with its automated lumber grading system. This type of data integration improves the accuracy of the grading process even as it accelerates it.
Grace shares additional benefits of the Omega system, “Another plus to having the Omega is the Wagner Meters’ service. Whenever I call them with a question or issue, they respond quickly. About 95% of the time we can resolve any issue over the phone. They also regularly call and occasionally visit to see if everything’s running fine. Just knowing they’ve got my back gives me good peace of mind.”
Tony Morgan, Wagner Meters Senior Systems Technician, explains, “We’re always looking for ways to take advantage of advances in technology so we can offer our customers better products and greater production. As our customers’ needs change, we’ll continue innovating and providing the tools and resources they need to do their jobs well.”
Consistent Quality and Production Levels Keep Battle Lumber a Major Player
While lumber production is expected to grow and stabilize prices, there are always unpredictable variables. Continuing demand from China can help offset a slowing construction market in the United States, or … new tariffs on forest products can depress demand from China over the next year. Perhaps expected closures of sawmills across Canada may increase Canadian demand for U.S. lumber … or not.
The unpredictability of the lumber market is exactly why a large sawmill like Battle Lumber prioritizes staying at the leading edge of technological advancements. Using technology to maximize quality, yield, and operational efficiencies means Battle Lumber will always have inventory available for its customers.
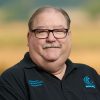
Tony Morgan is a senior technician for Wagner Meters, where he serves on a team for product testing, development, and also customer service and training for moisture measurement products. Along with 19 years field experience for a number of electronics companies, Tony holds a B.A. in Management and his AAS in Electronics Technology.
Related Posts via Taxonomies
Last updated on June 7th, 2022