Shelton Structures: Where Presentation Matters
1977, a new company opened for business in Shelton, Washington. “It was started by my grandfather and father, who called it ‘Shelton Structures‘,” said President Paul Ericson.
The business model focused on one product to begin with, but that didn’t last. “The product they made at that time was structural glued laminate (glulam) beams for both the commercial and residential housing markets,” Ericson continued. “In 1988, the company expanded when they entered the Japanese market, opening up a second plant in Chehalis, Washington.”
“In 1990, they went ahead and shut down the Shelton operation and consolidated everything into the Chehalis facility. This was a successful business up until the Japanese downturn around 1994. The decision to sell the glulam plant was made a couple of years later.”
Then they started down another road. “In 1994, my father started Shelton Lam & Deck, which was in a building behind the glulam plant here in Chehalis,” Ericson explained. “The primary product was laminated roof decking for both the residential and commercial market, which we still make.”
“Although decking was the primary product up until around 2007, when the market got worse we had to figure out what additional products we were going to make to survive the worsening construction market.”
Today, the company is more diversified in its offerings. “Our Lock-Deck™ product, which is a trademarked name, is still our primary product,” said Ericson. “The remainder is custom glulam beams and other engineered, glued products as well as various hardwood and softwood mill-work products.”
This diversification has been key to their business model. “We have and continue to look at ways to diversify,” Ericson said.
Bad Housing Market? No Problem!
While you may think that a downturn in the housing market would really hit Shelton Structures hard, that’s not necessarily true. “Although you will find our laminated decking product in custom homes, most of our decking is for the commercial market,” said Ericson. “The decking is used for ceilings and roofs, as well as floors and balconies. You will find this product used in churches, schools, public libraries, ski lodges, indoor pool enclosures, and wherever else the ceiling is to be not only a structural feature, but also a visual part of the structure.”
Asked whether wood paneling is part of the mix, Ericson nodded and said, “We run both solid and laminated tongue and groove patterns in both hardwood and softwood species. Our laminated decking is sold through our Lock-Deck™ sales office in Clackamas, Oregon. Our other products are sold through various wholesale distributors.”
The Importance of Moisture Control
As with many wood-centric businesses, moisture control through aggressive metering is important. “All of the lumber for our Lock-Deck™ production and our glulam beam production needs to be moisture-checked, so it goes through an in-line moisture meter, the Model 683i Wagner moisture meter,” said Ericson. “We’ll do spot checks. When lumber comes in, if we’re suspicious, we’ll check it to get some idea of whether we’re going to have a problem. We’ve got three hand-helds scattered around the plant just to do spot checking and it’s also a quick way to determine whether our in-line moisture meter is reading correctly.”
Electromagnetic wave technology meters from Wagner don’t have to pierce the wood, like meters using resistance technology. “We like the Wagner moisture meters simply because you’re not doing damage to the wood,” Ericson pointed out. “We don’t have the luxury on our products to be taking off a lot of surface once it goes into the moulder or planer, so we don’t want to have some pinholes in the wood. The guys with the [resistance technology] moisture meters with the needles would argue ‘Oh, that will clean up’, but not when you’re only taking a sixteenth of a cut off the face.”
After all, presentation is everything in this business. “Every part we make here is for an exposed application, whether it be a glulam beam, whether it be alder, whether it be a cedar solid beam, or if it was our laminated decking,” said Ericson.
As with the product line, the species mix is also diversified. “The predominant species here is Douglas fir, I would say 60%; probably 10% ponderosa pine and other white woods; 10% cedar, and the balance probably alder.”
How Long Does Your Moisture Meter Hold its Calibration?
When considering calibration issues, the tale of one Wagner moisture meter that hasn’t needed calibration since it was purchased in 1997 is instructive. “Yep, it still works, it’s still reading,” Ericson confirmed.

Free Download – How to Choose a Moisture Measurement System for Your Sawmill Buying Guide
“We can easily calibrate our hand-held with the calibration block that is supplied by Wagner, so we’ll periodically go out there and check what the in-line moisture meter is reading against our hand-held moisture meter, which is probably not the recommended way, but that’s how we’re doing it. The other way we would know if it’s not working is if that wood comes through our presses with the RF generators. We’d know immediately if there was a moisture issue because of arcing. The idea is to detect for high moisture before it goes to the presses.”
Looking Toward the Future
Although the future is uncertain, Paul Ericson is cautiously optimistic. “Hopefully the market will continue to improve,” he stated. “Regardless, we will continue to look for new opportunities and products to make no matter what state the construction market is in.”
Wagner Meters products have proved reliable for many years at Shelton Structures. Give us a call to find out how we can help you deliver quality at a great price!
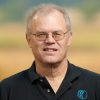
Larry Loffer is a senior technician at Wagner Meters, where he has over 30 years of experience in wood moisture measurement. With a degree in Computer Systems, Larry is involved in both hardware and software development of wood moisture measurement solutions.
Related Posts via Taxonomies
Last updated on June 6th, 2022