What Is Kiln Drying? The Reasoning Behind Drying Wood
Kiln drying is a standard practice in wood production mills and serves to efficiently bring green lumber moisture levels down to “workable” range–moisture content levels that will not end in the myriad of problems that can be caused by excess moisture levels in wood.
These problems include warping and twisting in dimensional lumber, binding or kicking during machining, buckling or crowning in an installed wood floor, and adhesive failures in finished products.
Moisture-related problems can cost millions of dollars in damages each year. Kiln drying is a first step in bringing all wood products to moisture content levels that will be subject to minimal moisture-related damage.
What Is Kiln-Dried Wood?
Kiln-dried wood is wood that has been dried in an oven (kiln). With a kiln, you can control the environment such as temperature, humidity, and steam levels for a set period of time. Allowing you to dry wood to the desired moisture content faster than air-drying.
What Is Air-Drying?
Air-drying lumber simple means to stack lumber and expose it to the outdoors. Depending on the species of wood and desired moisture content the air-drying process could take several months to almost a year. Make sure to properly stack the wood for sufficient air circulation.
The Kiln Drying Process
When trees are felled and brought to a lumber mill, the first step is usually to debark and sort the logs by species, size or by end-use. Logs destined for wood flooring, for example, are then sawn into rough boards of the required dimensions. These are often edged or trimmed for length before they are dried.
Drying can be done either by air or kilns, which use circulating heated air to more rapidly remove the excess amount of moisture from the wood. Each charge (or kiln load) is sorted by species and dimensions to optimize the process and to ensure that the final moisture content levels are even across the charge.
After the kiln dried lumber has reached the correct moisture level for that species, it is sent through the planer and planed to its final dimensions, sorted to grade and shipped out. For wood flooring or other specific end products, the wood is typically shipped to a manufacturer for further planing, processing, and finishing.
Mills and manufacturers alike invest time, money and training into their drying processes to provide optimal grade products at the correct moisture levels for their customers.
So if the wood leaves the kiln at the required moisture content level, the moisture content process is complete, right? It might seem feasible, but in reality, kiln drying is only the first step of a wood product’s life-long interaction with moisture.
Kiln drying significantly reduces the moisture content of green lumber, but there’s more to be considered.
Moisture Past the Kiln
The reality of wood’s nature, and indeed, part of its attraction over the centuries, is that it is a hygroscopic material. Until it is fully sealed, wood constantly interacts with moisture in its environment and will absorb or release moisture as necessary to find a balance with its environment.
Examined closely, wood’s long, hollow cell structure means that each board is composed of bundles of long cells (think of a stack of drinking straws). In a living tree, those pathways function to move moisture and nutrients from the roots to the branches and leaves of the tree.
Once the tree is felled, those pathways begin to lose that moisture as the wood dries. That moisture is naturally not replaced as it would be in a living tree, and the wood’s moisture level will drop considerably as it dries.
The kiln drying process helps to draw that moisture out while minimizing the damage to the wood that rapid changes might cause.
Why is that so important?

Free Download – How to Choose a Moisture Measurement System for Your Sawmill Buying Guide
“Wet” or green wood does not function well for anything from campfires to building materials. Its performance as green lumber can be unpredictable because of that inevitable moisture loss after the living tree is felled.
As it dries, wood can twist, crack, warp, and shrink in its physical dimensions, making it less than ideal for buildings, flooring or woodworking. It’s an ongoing cycle in wood.
Think of a sponge. When a sponge is wet, it holds moisture in each hole or cell. As it dries, it not only releases that moisture, it shrinks in size.
If it has been trimmed to a functional shape, like a rectangle, it may twist or curl as it dries. It does not, though, lose its capacity to reabsorb water when it is present. The sponge’s physical dimensions will change each time it absorbs and releases moisture.
In the same way, wood may have much of its moisture removed during the kiln drying process, but it does not lose the ability to reabsorb moisture that is in its environment. It might be a direct water source, moisture in adjacent material or even humidity in the air; wood’s cellular structure will be ready to absorb any moisture it contacts.
Even when wood has been kiln-dried, it may have a documented moisture content level, but at any step of the process after the kiln–transportation, manufacturing, storage or installation–it is possible for wood, even manufactured wood products, to lose additional moisture (in a dry environment) or re-absorb ambient moisture, altering its moisture content level and possibly even its dimensions.
If that moisture increase or decrease happens, for example after a wood floor has been installed, buckling, crowning, gaps, or other moisture-related problems can jeopardize the floor’s integrity. Any completed wood project or product can be jeopardized by moisture imbalances in the wood used.
What’s the Solution?
Just as lumber mills and manufacturers invest in accurate wood moisture content management tools and systems, each step of a wood product’s lifespan requires moisture content measurement.
Continuing with our wood flooring example, it is just as important that the flooring installer allows each board bundle to acclimate to the job site environment before installation begins as it is for the manufacturer to make sure the moisture content is accurately monitored before it leaves the plant.
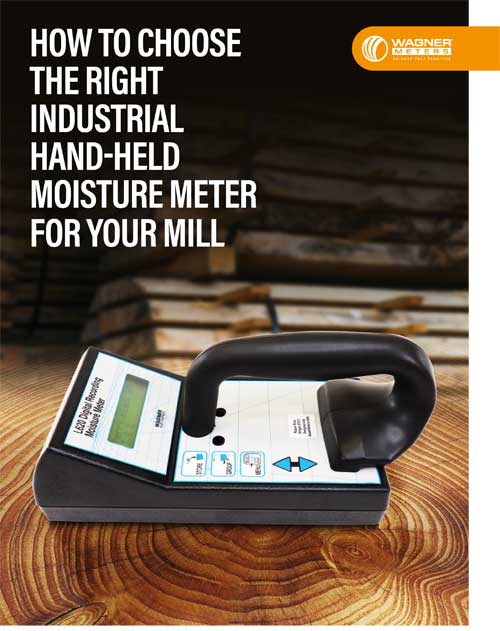
Free Download – How to Choose the Right Industrial Hand-held Moisture Meter for Your Mill
An accurate wood moisture meter can provide quick, accurate and reliable monitoring of wood flooring to ensure that the installed floor will not suffer from moisture-related problems like those identified above.
Wagner Meters’ non-damaging line of pinless wood moisture meters can take measurements as frequently as necessary without marking the floorboards or causing imperfections that will become visible once the finish is applied.
With accurate and current wood moisture content measurement, the flooring can be installed with assurance, finished for long-lasting, and durable use.
From forest to final finish, wood’s relationship with moisture must be understood and accurately measured, not just in the kiln but at each step of the way to its final use.
Take accurate moisture readings with the best pinless wood moisture meter in the industry.
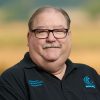
Tony Morgan is a senior technician for Wagner Meters, where he serves on a team for product testing, development, and also customer service and training for moisture measurement products. Along with 19 years field experience for a number of electronics companies, Tony holds a B.A. in Management and his AAS in Electronics Technology.
Related Posts via Taxonomies
Last updated on June 7th, 2022
Thank you for your answer, Ron. This validates my fear of using conifer wood based cat litter; as Phenols are toxic to cats. It’s too bad because otherwise it is a great product.
Does kiln drying remove phenols from pine and other conifer woods?
According to some studies, it appears that all phenols are not removed, but they will migrate within the lumber during kiln drying.
Suggest this study: https://www.ncbi.nlm.nih.gov/pmc/articles/PMC6179209/
Once Kiln dried to about 19%and then sealed to remain near that content, what is the effective insulation value of dried woods to be used in a log home? I am not sure of the log wood yet, but likely pine or other evergreen. I need to confirm if a log home is worth the effect if it is not thermally that efficient. I am considering a log home by Southland or Golden Eagle log home manufacturers, both using kiln-drying of logs. Do you have any insulation values for various woods if Kiln dried?
John,
Unfortunately, Wagner is not an expert in R-values of insulation or logs, but rather we major in moisture measurement technology for building materials. I did a little research and found this; trust it helps you out:
https://www.precisioncraft.com/log-homes-blog/energy-efficient-log-homes/#:~:text=In%20other%20words%2C%20the%20insulating,%2Dvalues%20of%2012%2D16.
Hello,
I recently purchased a slab of black walnut (2” thick) that I intended to use for kitchen shelving. The wood was originally cut about three weeks ago. I’m wondering if it is necessary to dry the wood. For such a small project I’m ok with minor cracks or warps over the years, but would prefer to avoid major changes in the shelves. I plan on using a polyethylene to seal it.
Assuming that the wood does need to be dried, would it be appropriate to take it to a kiln dried firewood processor or is there another route that you’d recommend?
Scott,
I would try and have the slab reach Equilibrium in the area it will be used or take it to someone that could kiln dry it. I understand small cracks may not be a major concern but warped shelves may not allow your dishes to set level. I hope this helps. Thanks for writing in.
Rick Cerieri, yes, I have heard this too but cannot confirm it (Can someone else?). I heard that in kiln drying the cell walls actually rupture as moisture is removed. After that, the wood more quickly takes on and also loses moisture (avoiding an imbalance) and thus reduces the tendency to crack. I would be very interested to know if this is really true.
Hello, Im in Phoenix az and am a firewood vendor. I have a friend who wants to get into milling wood , he just bought a solar kiln someone made. The build is a copy of a solar kiln made at Virginia tech for whatever reason. Obviously Az weather is far different from Va. My friend said that he’s been told by other local mill guys, wood dries too fast here in the summer and the solar kiln is the way to go. When i spoke to the original owner of the solar kiln he said its 5 times faster than air drying?
I have no background in kiln dried lumber and I’m confused by the contradicting ideas that a solar kiln is superior to air drying because air drying is too fast If the solar kiln is 5x faster?
Can you shed some light on this?
Is talc used to kiln dry wood? If so how is this applied?
RK,
I am unaware of any kiln-drying procedure that utilizes talc
Hello,
Long ago, I had a disagreement with a guy about kiln dried versus air dried lumber. I argued that they were not the same because I read an article that said kiln drying changes the cell structure of lumber that air dying doesn’t do. He insisted they were the same, and I insisted they were thus different.
Who was right?
Rick
Hello Ron, Eric or Tony,
Could you please send me a list of kiln operators that I could use to provide me a quote to dry western red cedar timbers? I am building a porch addition and trying to alleviate the splits or checks that are common when using ‘green’ timbers. The quantity of timbers that will need to be dried is – (7) 8 x 8 x 8′ Rough Sawed & (1) 8 x 8 x 12′.
Thanks
Hi Tom,
Please give me a call at 541.582.0541.
Thanks.
hello, i recently obtained newly cut red pine boards 5 x 35cm x 12 feet. i need to dry this wood to make bar tops with. i asked around for companies who provide the service of kiln dry and no luck. would you have a suggestion for me. how much time do i need to air dry the wood before i can make the tops. I reside in the Ottawa/Gatineau area.
Jean,
Please give me a call at 800-634-9961. Otherwise, if you’d like you can provide me with a number to get a hold of you at.
Thanks.
Hi Ron,
After the wood has been used as intended, how does one preserve this wood as regards an increase in the moisture of the environment and other adverse condition such as decay.
Thanks
Hi Joe,
The environment the wood is in must be maintained at a level of relative humidity so that it doesn’t change significantly. If that’s impossible, finishing the wood or treating it in such a way that it can’t absorb or transfer moisture is the next thing to consider.
Hello,
do you know how much money a mill usually spend in kiln sticks?
Hi! I recently brought back some 8/4 kiln birch to my shop and had serious shrinkage problem whit it, i didn’t own a decent moisture meter at the time (i have a Orion 930 now!) i don’t usually pay real attention to moisture level since i never had any problems with it before. We were still in winter time at the time so i suspect maybe the change of temperature during the transportation (enclosed trailer) may had created the problem, if the curing was fine from the kiln should i expect a big moisture variation during the few hours it took for transportation and if so what time laps am i looking for before it goes back to correct workable moisture level ?
Thank you!
Gino,
It appears the wood was too high in moisture content compared to the moisture condition in your shop (I assume from your email that it shrunk in your shop).
Hello!
Does kiln drying remove any insecticides that wood has been treated with?
Even with kiln drying, unless you completely dry out the wood (which of course you should never do) there will still be some moisture, and I presume insecticide residue.
Hi there. I learned recently that talc is used in wood curing. Is this something that is done during the kiln drying stage or after depending on the manufacturer? Are there any other chemicals used during the kiln drying stage?
I have never heard of this, so I contacted several kiln operators and got the same answer. Talc is not used in the drying or curing of wood. At least not in softwood kilns. Also no chemicals are used in the drying stage. Some mills do pressure treatments or spray pesticides or moldicides on their lumber, but always after the lumber has been dried.
Hi Ron,
I work at a company that is storing and moving high value sensitive energy products in crates. We recently made this change and find the inside of shipping containers can be drenched with water within a week of storage. The wood we use is IPPC heat treated. Should we also be sourcing kiln dried (KDHT) wood? Would that help or eliminate the problem or is this just the reality of using wooden crates in a variety of altitudes/continents?
Thanks!
I highly recommend you review this document, especially the Appendix: https://www.ippc.int/static/media/files/publication/en/2017/02/ISPM_15_ED_En_2017-02-10.pdf vie Even if the moisture content of the crates themselves is below 20% MC, the crates may end up being exposed to adverse conditions causing higher-than-acceptable moisture content and even condensation, therefore purchasing KD lumber, or crates made from such may not solve your problem.
Wagner counts some of the largest, most-respected pallet manufacturers in the world as customers of our handheld moisture meters, but again, just because there is strict MC quality control at the pallet/container manufacturing level may not assure that the pallets or containers end up with unacceptable moisture. Obviously, wood is a hygroscopic material that will pick up or give up moisture depending on its environment, and relative humidity change is the main factor.
Can you use a dehumidifier to dry your wood effectively?
I am asking because I started working for a custom drum builder (musical instruments) and we are having a problem with the drums shrinking and expanding after they have been milled and even after they have been assembled and shipped to the customer. After we get the wood from a covered but open shed and plane the wood it is then put in a room with a dehumidifier for a couple of days. It is then left in one of the shops which are not climate controlled or sealed from the elements as it goes through the different stages (cut, angled, glued, milled, painted or lacquered, dried, assembled). My fear is that we are not drying the wood correctly and that is why we are experiencing the problems. It seems most times that the drums warp at some point and one part of the drum diameter can be up to an eighth of an inch larger that its opposite side. And while the cabinet building part of the company can get away with changes like that, the drum building side cannot.
Any help or a point in the right direction would be greatly appreciated
Hi Darin –
There is dehumidification kiln drying technology: https://www.nyle.com/
Can you use a kiln to regulate timber to the same credentials as air dried?
Stewart,
Yes, as long as you can have the kiln environment match an air-dry environment.
I recently had a bunch of walnut kiln dried in boards and slabs and I brought it back to my workshop that is uninsulated and the moisture content came back to a higher level in the lo teens. Did I waste my time and money having it Kiln dried? Thanks for your reply as I’m trying to learn the process!
Brandon,
Was the wood checked with an accurate moisture meter when it was pulled from the kiln, and if so, what temperature was the lumber? What type, model and manufacture of moisture meter was used by the kiln drying company? Was the lumber protected from the weather when you were taking it back to your shop?
How long was it in your shop before you rechecked the moisture content? What type, model and manufacturer of moisture meter did you use?
Was the moisture content high in both the boards and slabs? What is the relative humidity (RH) and temperature in your shop?
Please call me if you wish; 800-634-9961.
Is this process helpful to remove the susceptibility of fungal and insect on rubber wood furniture for years like 20 years?
Hello, thank you for your comment. Please refer to this article on Heat Sterilization of Wood for more information. Thanks!
normaly how long does the wood have to be in the kiln drying, if you wanted to use it for furniture?
Drying rate of wood is dependent on a number of factors:
-Beginning moisture content
-Thickness of the wood
-Species
-Type of kiln
-Temperatures used
-How much air flow through the lumber stacks
The typical target for moisture content % in North America for lumber that will be used in furniture is 7%-8%. Our red oak species that is 2 inches thick, starting from very green (about 70% moisture content) might take 30 days of drying time. This species, as with others, must be dried carefully (not too fast, but controlled).
Is the process of drying woodworking lumber (dimensional lumber) different from drying firewood? Cracking is not an issue in firewood, but is it the same process, the same kiln?
Thanks.
Brian, the goal is the same: exposing the wood to a drier environment, so it will dry down to the appropriate moisture content. Obviously, you don’t have to be as careful with firewood.