Solar Dried Lumber Moisture Concerns – Solar Kiln
Because they capture the energy of the sun, solar kilns are becoming increasingly popular for the hobbyist or professional woodworker who wants to dry his own lumber, and with good reason; dried wood sold at a lumberyard is expensive.
Greenwood, on the other hand, costs much less. However, air-drying lumber can take several months and can lead to warping and cracking before it can be used. Drying wood in a controlled environment requires much less time and allows the wood to contract without warping.
Solar-drying kilns are the simplest, cheapest, and safest way to dry green wood quickly, and they are good for the environment since they don’t generate CO² emissions. A solar kiln will dry the wood with a smaller chance of defects than air drying.
“And they won’t dry wood too fast,” says Dr. Eugene Wengert, an extension forest products specialist at the University of Wisconsin-Madison. “It’s pretty much a ‘set it and forget it’ system. You can just put the wood in there and almost forget it. It’s only near the end of the drying when you need to measure moisture content (MC) to determine if it’s time to stop the process and pull the wood out.”
A solar kiln can also dry wood of varying shapes, sizes, or mixed species and thicknesses in the same load. After the kiln is loaded, only minimal vent adjustment is needed while the wood dries.
Key Kiln Design Features
Dr. Wengert developed a popular and simple solar kiln design in 1978. It is often referred to as the Virginia Tech Solar Kiln because Dr. Wengert developed it while working at Virginia Tech. Although there are different solar designs on the market today, the Virginia Tech design is the kiln model considered the standard by which other kilns are built. Woodworkers can find instructions for this model and other similar designs online.
The initial investment for a solar kiln varies, depending on the size and the building materials. However, it pays for itself in the long run.
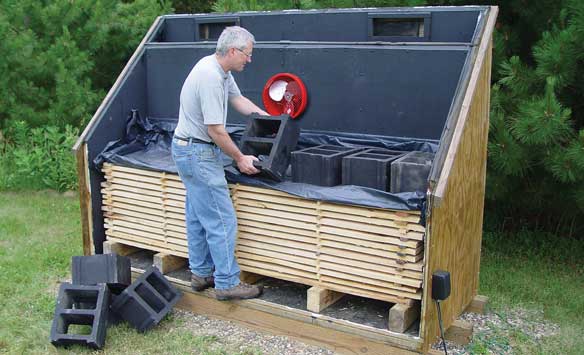
Photos by Joe Gohman
A small solar kiln normally dries anywhere from 800-1,000 board feet, although some can be downsized to dry only a few hundred board feet. A large solar kiln dries 1,500-2,000 or more board feet of lumber.
The Virginia Tech solar kiln can hold up to 1,000 board feet of 1-inch thick lumber per load and dry it in about one month of moderately sunny weather in the mid-latitudes of the United States. The kiln heats when solar energy enters the clear glazing and is absorbed on the black painted interior surfaces.
As air is heated in the collector space, one or more fans circulate it through the lumber, enabling it to absorb moisture from the lumber’s surface. When the evaporated moisture increases the relative humidity to where it gets too high in the chamber, it releases it through vents in the back of the kiln.
To alter the size of a kiln, one needs to keep in mind an important ratio: For every 10 board feet of capacity, one square foot of solar panel or roof area is needed. If the kiln has too much solar panel area, one risks the wood drying too fast, causing the wood to check and split. However, if there’s not enough solar panel area, there’s the risk of never being able to dry the wood below 15% MC.
In order to circulate air through the stack of wood, it’s necessary to install an electric fan. If a larger kiln is built, two or more fans will be needed for optimum airflow.
Roof angle also is important. To figure the proper angle, one needs to determine the latitude of the kiln. The latitude number is used for the pitch of the kiln roof.
For example, in Minnesota, the latitude is about 45 degrees north. In that case, the solar panel would be mounted at a 45-degree angle facing south. If used during the winter months, the angle should be increased by 10 degrees (in this case, to 55 degrees), since the angle of the sun changes from summer to winter.
Interested in building a solar kiln? Review the following magazine article about building a solar kiln.
Get the most accurate wood moisture readings from an Orion pinless moisture meter.
Moisture Readings
Solar drying time for lumber can vary. For instance, drying time in the summer takes less time than in the winter. Also, the drying time for 2-inch lumber will take longer than 1-inch material.
Woodworkers first learning to dry lumber, especially lumber thicker than one inch, should monitor MC daily to avoid drying too rapidly. It’s important to monitor drying speed by measuring the MC of the sample boards and comparing the daily rate of moisture loss with the “safe rate” for that species.
There are tables available that list the safe rates for drying 1- or 2-inch thick lumber from different species. The safe rate refers to the loss of moisture in one day. Safe rates must be followed until lumber MC drops to 20%.
Although moisture meters don’t work well when the MC is above 30%, the design of the kiln is such that it normally won’t allow the wood to dry too fast. Still, when just learning to dry lumber in a solar kiln, it’s best to monitor the process to avoid any unforeseen problems.
Exceeding the safe rate drying speed for a given species can cause defects in the lumber. If drying is too fast, part of the roof should be covered, or the fans turned off and the vents closed during the hottest part of the day. Although the temperature will likely rise inside the kiln, the trapped air will quickly reach 100% of its capacity to hold water and the lumber will stop drying.
It’s also important to identify sample boards at the start to determine MC loss rate. These are boards that may have started out with a higher MC than the rest of the load were cut more recently than the others or are a little thicker.
“If you check the sample pieces and they’re too wet, you’re going to continue drying,” says Dr. Wengert. “You want to make sure your sample pieces are dry enough before you stop drying. It doesn’t really matter if half the load is ready to be pulled out.”
“So don’t pull the load based on the average. We usually pull the load based on the wettest pieces. The wettest has to be dry enough,” he adds.
Dr. Wengert notes that the Virginia Tech solar kiln was designed so that it wouldn’t allow the wood to dry too fast. However, if the kiln is only half full and the lumber inside is prone to cracking, such as oak is, it would be necessary to cover half the collector on the roof. Otherwise, there would be too much solar input for the little amount of wood in the kiln.
Moisture Meters
Moisture meters for kiln driers should meet all the specific needs you might encounter. A pin meter measures the MC of wood by running an electrical signal between the tips of two narrow metal probes that are inserted into the wood.
The major disadvantages of pin meters are the relatively small area tested with each insertion, their sensitivity to wood temperature, and the damage the pins do to the wood surface. The pins can also break or give inaccurate readings when improperly inserted.
Pinless meters use an electromagnetic signal to penetrate the wood surface. Their design lets users “scan” many board feet of wood simply and quickly. Because they don’t have pins, they do not damage the wood surface. They take readings at a fixed depth but do require sufficient pressure to give a correct reading. They may be susceptible to scratches or damage on the sensing pad as well.
“The best meter, however, is one that’s used,” says Dr. Wengert.
“If you’re drying wood and you’re going to make something of it, how much would you pay for insurance that it’s going to work right? Using a moisture meter will help you prevent it from cracking, warping, or splitting after you’ve made it. What’s that worth to you? Other than the initial investment, you only have to pay for the batteries,” he remarks.
Wagner Meters, one of the leading manufacturers of American-made pinless moisture meters, says that “an accurate knowledge of the interaction between wood and moisture needs to be at the very foundation of each project a woodworker undertakes.” If not, every project is put at risk.
Each professional Wagner moisture meter comes with IntelliSense™ technology, which allows accurate readings deep in the wood, unaffected by surface moisture. Wagner has meter models for woodworkers who need to measure wood moisture in all wood species–from the more common softwoods and hardwoods to rare tropical species.
Optimum MC Levels
For most softwoods, Dr. Wengert says a 10% MC reading is optimum for indoor use. However, he would accept a reading of 10.5% or even 11%, but not higher than 11%. To go any drier than 10%, the lumber begins to machine poorly. It’s acceptable for softwoods to be slightly wet for indoor use. The amount of shrinkage that occurs is minimal, he says. In other words, the machining benefits outweigh the little bit of shrinkage.
For hardwoods used indoors, the target MC is 7%, though a 6.5% or 7.5% reading is also acceptable.
For outdoor use, both softwoods and hardwoods should be dried to about 12% MC. However, the MC will vary if the wood is going to be exposed to rain or an outdoor sprinkler, or if it’s going to be in a dry climate such as in Albuquerque, a wet climate such as in Seattle or a coastal region. In addition, if the wood is to be used for exterior house walls where it’s protected from rain, a good average is 12% MC.
Summary
Solar kilns are ideal for the hobbyist or professional woodworker who wants to save money by drying his own lumber. Solar kilns are relatively inexpensive to build and simple to operate. They use the free energy of the sun, so they cost nothing to operate except for the small cost of electricity needed to run the fans. Additionally, they are good for the environment since they generate zero CO² emissions.
Although solar kilns are designed to keep the wood from drying too rapidly, it is wise to check the MC level, especially near the end of the drying cycle. It’s also recommended that woodworkers who are new to drying lumber in a solar kiln or who are drying wood thicker than one inch frequently check the moisture levels to prevent defects later on. A moisture meter is a woodworker’s best insurance for solar-dried lumber to prevent cracking, warping, or splitting in the finished wood product.
Check out these solar kiln instructions.

Troy Edwards is Technical Service Supervisor for Wagner Meters, Inc., where he oversees manufacturing, quality control and IT service for their electronic measurement products for the building and construction industry. Troy holds an AAS in Electronics Technology and has over 20 years’ experience in various electronic manufacturing and production positions.
Related Posts via Taxonomies
Last updated on February 9th, 2022
Wisconsin
I completed my Solar Kiln on September 15th and filled it immediately with a load of White Oak, Maple, Black Cherry, and White Pine. I built the kiln using the “Virginia Tech” plans, well the concept of it at least as I tend to view other peoples plans as merely suggestions. All of the lumber I put in it was in the mid 20% range for M.C. after air drying in my barn since being cut this last winter. After a month in the kiln my readings are about 7.5% for the White Pine, around 9% Maple and Black Cherry, and 11% for the White Oak. All of the boards are 2″ thick. My kiln gets HOT, maybe too hot. On a sunny 40 degree day I am still reaching temps over 120 degrees in the kiln. My plan is to keep the lumber in the kiln until deer season mid November, and reevaluate everything at that time as I have another load ready to go. So far, this has been a lot of fun. The kiln cost about $3000 for me to build, I used 8′ sheets of plexiglass for the solar screen and sided it with pro-rib metal siding, so I was on the high side for cost. I am not a wood worker, however I will be retiring in a few years and plan to get into it first as a hobby and then potentially as a business. I was surprised how many local wood workers were interested in buying boards from me when word got out that I had built this kiln, I think it will pay for itself in a few years just from selling boards. I built the kiln at 12′ x 8′, 45 degree angle for the glass, and the kiln is about 12′ high. The boards I am drying are 9.5′ long, 2″ thick, and anywhere from 12″ to 18″ wide and the ends are sealed. I hope this information helps.
Why not use a concrete floor and use it as thermal storage to keep the night time temperatures a bit higher and reduce condensation from potentially staining the wood?
Mike:
Not a bad idea as long as you constructed the concrete slab with a vapor retarder directly beneath, allowed more than enough time for the concrete to dry, and elevated the wood off the concrete to ensure proper ventilation. Also, concrete done correctly drives the cost up and makes the structure more permanent, which may not be as desirable for some.
Thank you so much for sharing this with us!!!!
Thank you !
I am curious how this Kiln would work in central ohio
I recently purchased a solar kiln built from
The Virginia Tech plans. I live in Phoenix AZ will it be too hot here to use this kiln?
Hi Jerrod,
Here is a quote from Gene Wengert, Author of articles in Sawmill & Woodlot and books: Drying Hardwood Lumber; VA Tech Solar Kiln; Sawing Edging & Trimming Hardwood Lumber.
He literally wrote the book on the VA Tech kiln:
“If there is wet lumber in the kiln and it is drying, then the lumber is using the heat to evaporate water. A kiln that gets really hot is not efficiently using the solar heat. In general, 20 – 25 F warmer in the kiln than outside is good for wetter lumber. As the lumber gets drier, the heat can go up to 30 – 35 F hotter than outside, which means that the lumber is drying more slowly, which does happen under 15% MC. Of course, a kiln will be hotter with better insulation and cooler with air leaks or wide open vents.”
Bottom line is I do not believe it is too hot in Arizona for drying lumber in a solar kiln.
Commercial kilns are generally much hotter than the ambient temperature:
Temperatures inside the kiln range from 120 to 190 degrees F, depending on the stage of drying. Although there are kilns in which temperatures reach up to 240 degrees F, they are usually limited to softwoods that dry very easily and low-value hardwoods.
I am interested in building my own solar klin in Uganda (on the equator). Are there any implications beyond putting a roughly flat roof…?
Here is a link to plans for a solar kiln. There are some very good tips on the design aspects and it also addresses the pitch of the roof in relation to your geographical location.
http://pubs.ext.vt.edu/content/dam/pubs_ext_vt_edu/420/420-030/420-030_pdf.pdf
I’ve been trying to find the plans for the larger version of Virginia Techs kiln, but have had no luck. Any chance you could direct me to it?
All references to the Virginia Tech 2000 board foot kiln seem to have disappeared from the web. I suggest contacting The Department of Forest Products at Virginia Polytechnic Institute and State University or trying to find the book:
“Solar Heated, Lumber Dry Kiln Designs: A Discussion and a Compilation of Existing Solar Heated Lumber Dry Kiln Designs” by Eugene M. Wengert, Luiz Carlos Oliveira
Department of Forest Products, Brooks Forest Products Center, Virginia Polytechnic Institute and State University, 1985