Custom Wood Harmonica Microphones Deliver a Sound That “Blows ‘Em Away”
“These mics are a work of art…and man, the wood makes the tone just drip out…warm as the Sunflower River in Clarksdale, MS, in July. And the piano finish is so smooth you can see yourself in it.” – Deak Harp, Blues Harmonica Musician
They are comfortable to hold, easy to use, and incredibly lightweight microphones made from one or more exotic woods and hand-rubbed or lacquered to a high gloss. To the many blues musicians who perform with one of these customized beauties with a huge, warm sound, they are pure gold.
The man who makes them is Greg Heumann, perhaps the only one in the world doing so. Although a few others have tried making wood mics, they never got very far with them.
“I think many people underestimate how much work is involved, and not just in making the mics, but all the other aspects of running this kind of business,” he says.
After having crafted more than 400 wood mics, Heumann says he is certain nobody else has made more of them than he has.
Heumann works out of a garage converted to a combination machine shop, wood shop, and electronics lab. There, he uses his skill as a woodturner and his love of music to handcraft beautiful one-of-a-kind wooden microphones for the who’s who of the music world.
His clients include Grammy award winners Charlie Musselwhite and Mark Hummel, as well as Rod Piazza, Rick Estrin, Kim Wilson, jazz artist Toots Thielemans (perhaps the most famous harmonica player in the world), Steven Tyler of Aerosmith, and Willie Nelson’s harmonica player for the last 37+ years, Mickey Raphael.
“My products are in use by professionals and amateurs all over the world,” Heumann says.
It’s a labor of love he’s been doing since 2004. That was the year he started making wood mics through his company, BlowsMeAway Productions.
Heumann previously worked in Silicon Valley as a technical marketer for Unwired Planet, the company that allowed mobile devices to connect to the Internet. Cashing out early, he moved to the small town of Geyserville, located about an hour and a half north of the Golden Gate Bridge in California’s scenic wine country.
For Heumann, the move to Geyserville was a dream come true.
Four years earlier he had purchased property there overlooking this quaint town of 1,600 residents and the surrounding countryside. Originally used for weekend getaways, he says he always dreamed of one day living there.
When that dream finally came true, he parlayed his boyhood experiences into a profitable business.
As a young boy, Heumann loved watching his father use a metal lathe and milling machine. Although he realized later that he didn’t learn much back then about using a lathe, he taught himself the skill when he started his business of making metal volume control products.
Music was also another facet of his early life. He began playing the oboe in the second grade and played through college. But when he hit his 40s, he picked up the harmonica and realized, “I should have been playing the blues all along. It’s the music that moves me.”
To take his mouth harp playing to the next level, Heumann took the Harmonica Master Class from renowned blues harmonica educator Dave Barrett at the School of The Blues in Morgan Hill, Calif. Soon after, he started playing in a five-piece modern blues band called Bluestate.
He recalls using an old 1950s microphone in his early performances. Made of metal, “It was heavy and clunky, not easy to work with my small hands,” he commented.
That’s when he decided to construct a new type of microphone, one better suited for his needs than the industrial microphones in vogue.
Since he was already skilled with the metal lathe, he decided to construct a microphone from wood. With the help of his dad, the wood mics he created were considerably lighter, more comfortable to hold, and yielded a richer, warmer tone than traditional metal mics – all valuable qualities to performers.
Pleased with the performance of his new mic, Heumann began asking others to give it a try. The first professional he approached was none other than blues legend and six-time Grammy award winner Charles Musselwhite, who also happened to reside in Geyserville. Musselwhite tried it and loved it.
“Charlie now has three of my mics and plays them regularly on tour,” says Heumann.
Soon after, he was crafting customized mics for both professional and amateur performers from around the globe. All rave about their custom-made wood mics.
Blues singer Mitch Kashmar says his mic is ‘so light it almost dissolves in your hand.’
Blues veteran Rod Piazza coos, “Not only is it gorgeous in appearance, but the feel and tone of the mic are as dynamic and punchy as you would want.”
And Mickey Raphael, Willie Nelson’s harmonica player, declares, “This mic blows me away.”
Wood Selection
Heumann’s microphones are made from a variety of beautiful, and in many cases, stunning wood species. He especially favors cocobolo, a Central American hardwood that comes in a kaleidoscope of different colors, and burl maple, prized by craftsmen for its swirling ring patterns.
He also uses many other exotic woods such as Gabon ebony, black and white ebony, East Indian rosewood, Burmese rosewood, Yucatan rosewood, Malaysian blackwood, kingwood, zebrawood, marblewood, burl walnut, curly maple, canarywood, redheart, spalted tamarind, yellowheart, purpleheart, and wenge, among others.
Most of these woods he buys from his local Woodcraft store, a place he shops every couple of weeks. For woods he uses a lot, like cocobolo and burl maples, Heumann has other sources he favors.
Occasionally, a customer will send Heumann a wood with sentimental value attached to it. One customer, for instance, had him make two mics from walnut he recovered from his grandmother’s house during a rebuild. He wanted each of his sons to have one.
Another customer had his mic made from burl madrone – a wood he had saved for 40 years. Still, another had his mic’s wood and design match his favorite vintage Hawaiian surfboard.
Since each wood is different, each has its own peculiarities and challenges. Burl maple, for instance, tends not to turn to a nice surface and can tear out. However, because Heumann has worked with it so much, he’s developed special techniques to deal with it and other troublesome woods.
One wood he likes to avoid is lignum vitae. When one customer wanted him to make his mic from this wood, he says he had a bear of a time getting it to take finish.
“Even though I’m used to working with woods like cocobolo that people will tell you are hard to finish, I have no trouble with it. The lignum vitae was impossible. I use a shellac-based sealer, which is about the most forgiving sealer there is. But on this wood, it would bubble and/or not set up hard when dry. Then I had trouble getting lacquer to sit over it, which is also unusual,” he confides.
Although Heumann finally got the job done after much toil and sweat, he says the easy solution next time around is, “Don’t do that!”
Avoiding Moisture Content Issues
Every wood blank or chunk of wood a woodturner acquires will lose or absorb moisture from the air until it eventually reaches a state of equilibrium with its surroundings. Purchasing wood from a lumber yard or wood store doesn’t mean the wood has reached this state and is sufficiently dry.
In fact, wood that holds too much moisture can ruin a project. In the worst cases, the wood can warp and splits can appear. Heumann knows this from experience and pays close attention to the moisture content of the wood he uses.
“I learned the hard way – by making mistakes,” he says.
“When I started making wood mics, I paid no attention to moisture content. But I’ve had woods change size and warp by as much as 0.50” over a 2.5” diameter – and that is more than enough to cause trouble for me. After a few mishaps, I figured I better start paying attention!” he adds.
Heumann then researched moisture meters on the Internet. He concluded that a pinless meter was better for his needs than a pin type. Plus, it left no unsightly pin holes in the wood.
“A pin meter will only tell you what’s happening on the surface. I normally use a commonly milled wood size called a rolling pin blank, which is 3 in. x 3 in. x 12 in. With a piece of wood that thick, the reading the pin meter provides is meaningless.
“My research led me to Wagner Meters. I now use a Wagner MMC220. It not only measures wood moisture in all wood species, including the rare tropical species I use, but it tells me exactly what I need to know. It has been worth every penny I spent for it in saved time and increased product quality,” he says.
While Heumann would love to work with wood that has only 6% to 8% moisture content, he says he doesn’t have that luxury.
“I’ve found if I use wood at 14% or less moisture content, I have no problems down the road due to post-turning shrinkage. A lot of woods at Woodcraft are at 20-25% when I buy them.
“And the rolling pin blanks are waxed all over to retard the natural drying process. That’s essential with hardwoods when they’re this thick. Otherwise, they’ll dry outside and crack while the inside remains wet. Even under the wax, if they spend a year or two in my shop, they may get down to 8-10%. But again – I don’t always have that luxury. The most important thing is to simply know what I’m working with so I can take appropriate steps,” he says.
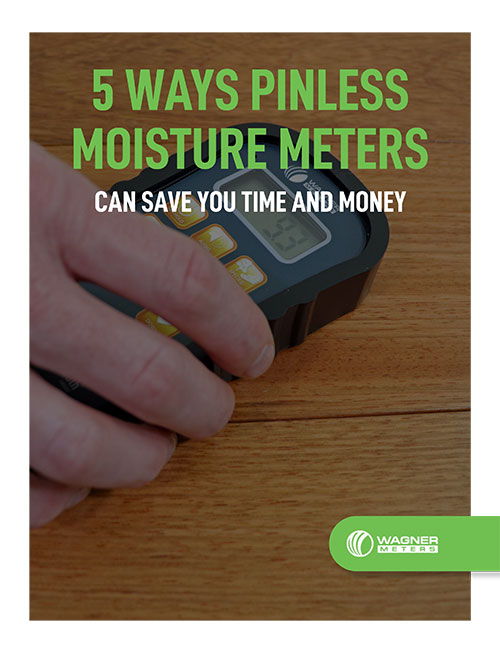
Free Download – 5 Ways Pinless Moisture Meters Save You Time and Money
Getting the Moisture Content Right
Heumann knows the consequences of not having the right moisture content level. He says there are two areas that are critical:
One is the fit of the aluminum grill on the wood shell. The grill is made within a few days of turning the shell, and he sizes it to be a very tight press fit. Inevitably, however, the wood will shrink after delivery and the fit will become looser.
“A little bit is okay, but a lot isn’t,” he says.
He recalls the time one mic came back to him with the grill measuring about .050” bigger than the shell. It didn’t look good and it didn’t feel good as there was a noticeable ridge at the intersection – right where a harmonica player holds the mic. It taught him a good lesson about staying on top of moisture content.
Part of playing an amplified Chicago Style blues harmonica is a technique called “cupping” the mic – achieving a relatively airtight seal between the mic, hands and the harmonica. That has a huge effect on the player’s tone.
“In order to get there we squeeze the mic fairly hard in our hands, so any bumps or ridges can cause discomfort. As long as the wood is dry, the grill and shell will remain exactly the same size. If not, it can be a problem,” he asserts.
The other critical area is on those mics with the Stealth Volume Control option.
“The degree of precision required on these mics means holding several machining steps to within a thousandth of an inch or so. The gap between the knob and the rear of the shell is only .01” – and if it isn’t perfectly centered and perfectly on axis, it will rub against the shell, or appear to wobble when turned.
“I actually make a metal bushing to press into the wood knob to help maintain this alignment. I also have to ensure that the inside rear of the shell is perfectly flat so that the volume potentiometer remains perfectly perpendicular when mounted. If the wood shrinks or warps, even a little bit – it might not look or feel so nice,” he says.
Handling Wood Defects
Once a piece of wood is properly dried and turned, it will be very round and will stay that way. Because of that, Heumann says he doesn’t have to deal with some of the common wood defects – like bowing or cupping.
But as for color variations, knots, insect holes – he loves them.
“That’s what makes each mic unique. As long as there is no threat to the mic’s structural strength, I may leave them as is,” he says.
But in some cases, with burl maple or sometimes redheart, there can be a big enough hole or knot that he will fill it in with some sort of inlay material. He fills in smaller defects with clear glue (cyanoacrylate) before finishing so the defect still shows. This prevents the defect from being felt and blocks air or moisture from getting into the wood.
Heumann says that because these pieces are fairly small (about 2.3” in diameter and 2.5” long), he always looks for wood with as much irregularity as possible. In other words, he prefers woods with either lots of contrast between colors in the grain (such as in cocobolo) or unusual grain patterns (or none at all) like with burl maple.
“I do look at the wood specifically for these things before turning and try to orient it to highlight those features as much as possible. Anyone who has turned wood will tell you that a round piece of wood is going to have at least some portion of its circumference that’s more interesting and another side that is less so. Because these mics have a top side and bottom side, I try to orient them so the boring part is at the bottom,” he states.
400 Mics and Still Improving
Heumann has already created more than 400 mics and the count continues to grow. However, even after that many mics, he says he’s still discovering ways to make them better, faster, and more beautiful.
For instance, he now makes his basic mic – involving the creation of the shell and grill, installation of a connector and microphone element, and a hand-rubbed finish of shellac and wax – in roughly three hours, or about one-fourth the time it took when he started.
Of course, those mics equipped with various options – such as the stealth volume control (where the tail of the mic becomes the volume knob), eye-catching inlays like aluminum powder or red, gold, blue, and turquoise granules, and personalized grill designs engraved with the artist’s initials – take several hours to complete.
Furthermore, those mics completed with his top-of-the-line finishes, what he calls, respectively, the “violin” and “piano” finishes – take a couple of weeks. Those finishes involve several coats of a shellac-based sealer followed by as many as 10 coats of clear lacquer.
Virtually all of Heumann’s mics are made to order. In fact, he offers a “design your own mic” section on his website that lists the various options and prices. Customers can also view pictures of his creations to see the types of woods and grill designs.
The starting price for a basic wood mic is $279. Much of that cost is the element inside that actually converts the sound into an electrical signal. Heumann collects and recycles vintage elements from old microphones because they sound better than modern ones.
The average mic runs about $450, while one with lots of options and a “crème de la crème” rare vintage element runs close to $900.
Heumann tests each microphone for sound, reliability, and overall quality before presenting it to his customer.
“I realized recently that means I’ve probably played through more harmonica mics than anyone else in the world!” he says.
Heumann’s mics are guaranteed for a year, and should any problem arise after that, he’s more than willing to satisfy his customers.
The Interest Never Wanes
Heumann confides he never tires of making these heirloom-quality mics and striving to make the next one better than the last.
Each one also brings him immense personal satisfaction – both in their creation and in seeing the joy they bring his customers.
And while he’s made hundreds of mics, he happily reports his interest never wanes.
“I love the surprises each wood throws my way. Each piece of wood is different and holds a surprise or two. And I like seeing things in them that might or might not be there.”
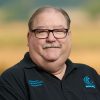
Tony Morgan is a senior technician for Wagner Meters, where he serves on a team for product testing, development, and also customer service and training for moisture measurement products. Along with 19 years field experience for a number of electronics companies, Tony holds a B.A. in Management and his AAS in Electronics Technology.
Related Posts via Taxonomies
Last updated on June 29th, 2022
Wow. For some reason, I never saw this article when it was published. Thank you, Tony, for a well written and accurate article. Having been around that block a few times I can tell you that often is not the case! But you listened well and did a really nice job of telling my story. Today in 2020, I have sold about 800 wood mics (and thousands of mics overall as the wood mics are one of 4 lines of mics I manufacture in my garage.
Cheers!
Greg Heumann