Wood Flooring Moisture Content Affected from the Ground Up
The moisture content of wood flooring can always change over time or with changes in the environment. When working to prevent moisture-related problems with wood flooring, there are multiple layers that can contribute to moisture issues immediately or down the road. Simply acclimating and installing the flooring product itself is only one step in a series that should be included when installing wood flooring products.
The Concrete Slab
“I’m a wood flooring specialist; why would I need to know about concrete?”
For a wood floor installed over a concrete slab (whether that includes separate subfloor or not), the moisture picture in the concrete slab can have real ramifications for the finished floor. If a new slab has not dried completely to finished specifications, that moisture will continue to wick up through the surface of the concrete and can cause anything from adhesive failure to wood warping or cupping. If an older slab has developed cracks or moist patches, those can also work their way to the surface and provide an avenue for moisture to compromise a wood floor. Even with the usual vapor barrier, moisture can still be an issue if the slab has not properly dried. So it pays to have an understanding of concrete moisture testing.
Concrete moisture conditions are most reliably established with relative humidity (RH) testing that uses in situ probes. Other test methods, including calcium chloride testing or the poly-film test, have proven problematic in the past and are slowly being discontinued by organizations like the Maple Flooring Manufacturer’s Association. Other varieties of meters, like moisture meters for concrete, might, at times be helpful in taking relative readings in existing slabs to help determine the most likely areas for the necessary further testing with true quantitative moisture testing methods (ASTM F2170, in-situ RH testing, etc). Surface concrete meters do not provide an in-depth picture of moisture conditions within the slab, therefore, true quantitative testing must be done.
While you, as the flooring contractor, may probably not perform the RH testing, it pays to check what the job specs have called for, and what the test results have shown before beginning your installation. Moisture problems in the concrete slab may not ultimately be your responsibility, but left unchecked they still, unfortunately, will often end up becoming your problem.
The Wood Subfloor
Improper moisture conditions in a wooden subfloor can lead to moisture-related issues in a finished floor. Two types of wood flooring moisture meters are often used to determine the moisture content (MC) of wood subfloors: the pin-style meter and the pin-less (or non-destructive) meter.
A pin meter measures the moisture content of wood by running an electrical signal between the tips of two sharp probes that are inserted into the wood. They can indicate moisture levels through either analog or digital displays, and can also include a range of pre-programmed settings for different wood species, or a table for manually adjusting the readings to the required species of wood. One advantage of pin-style meters (only those that use longer pins with insulated shafts) is that you can test at different depths in the wood. The major disadvantage is the relatively small area tested with each insertion, and the damage it does to the wood surface with each test.
Pinless meters use an electromagnetic signal to penetrate the wood surface and use that signal to measure the moisture content of the wood being checked. Their design lets users “scan” many board feet of a wood product simply and quickly, and of course, their pinless style means no damage to wood surfaces. Pinless meters can also take comparative readings through various finishes without damaging them, and are generally less sensitive to temperature. Pinless meters, like their pin-style counterparts, can be user-programmed for various species of wood.
With either style of wood flooring moisture meter, it is important to test several areas of a wood subfloor to be sure that the moisture conditions are acceptable for the final flooring installation. A good rule of thumb is that the subfloor moisture content should be within 3-4 percentage points of the flooring to be installed before proceeding.
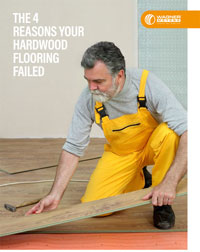
Free Download – 4 Reasons Your Hardwood Flooring Failed
The Flooring
Before installation, the flooring to be installed should also be checked with an accurate wood moisture meter. Several bundles should be opened and tested to ensure that the wood flooring is at the same MC throughout, and is compatible with the subfloor over which it will be installed. Like the wood subfloor, pin-style and pinless meters can give an indication of the MC to ensure a professional and long-lasting flooring installation. The advantage that pinless meters have with wood flooring is in their damage free measuring; no pinholes means no filling or sanding on the final floor. And of course, room conditions should also be monitored to ensure they are at, what will be normal conditions. Even a good flooring installation with adequate moisture testing might not overcome extreme changes in ambient temperature and humidity. And, allowing the wood products to acclimate to these normal ambient conditions is one of the best-recommended practices.
As the old adage says, “An ounce of prevention is worth a pound of cure.” At any stage of the flooring work, an accurate moisture meter is your best defense against moisture-related problems making an appearance.
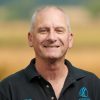
As Sales Manager for Wagner Meters, Ron has more than 35 years of experience with instrumentation and measurement systems in different industries. In previous positions, he has served as Regional Sales Manager, Product and Projects Manager, and Sales Manager for manufacturers involved in measurement instrumentation.
Related Posts via Taxonomies
Last updated on May 4th, 2021
We are in the process of moisture mitigation – a 2 yr old home had cupping of high quality engineered maple floor. All wood (subfloor and wood planks) were moisture tested and acclimated to the environment but concrete was not tested before the subfloor was put down. Concrete was poured on radiant heat pex tubing. All wood has been torn out and we are now drying and testing the concrete with probes for RH humidity. Have not found a a specific humidity percentage recommendation that is considered acceptable level to begin work again of subfloor and wood planks. Do you recommendation a particular percentage or at least a range?
Cheryl:
Thanks for the comment. I would contact the National Wood Flooring Association, at nwfa.org, for guidance on this question. They should be able to get you the information you desire.
Thanks,
Jason