Moisture-Related Damage in Shipping: Is It a Big Deal?

Image by hectorgalarza from Pixabay
Global commerce would barely exist without global shipping. According to the International Chamber of Shipping, shipping carries around 90% of global trade1 around the world. Containerized shipping2 accounts for 60% of all this seaborne trade.
The risk of goods being damaged as they sit in storage containers and spend days at sea is high. Moisture damage is one of those risks. Trade Risk Guaranty3 states, “About 10% of all container shipments must be discarded due to moisture-related damage.”
That means roughly 5% of global goods become a financial loss due to moisture damage that occurred during shipping. That’s a lot of money sinking to the bottom of the ocean. Worse, insurance rarely covers that loss.
You might assume that ocean water seeping into a container causes moisture damage. It can cause some, but it’s not a primary driver. Like the horror movie cliché, the main moisture threat is already inside the container. The greater risk comes from moisture present in the air and cargo. Changes in temperature and humidity can convert this moisture into liquid. This water is what will cause mold, corrosion, and other types of physical damage.
Excess moisture can cause food to go bad, electronics to malfunction, or building materials to decay. Even the presence of a bad odor, absent physical damage, is grounds for a buyer to reject a shipment. The first step to protecting containerized goods from water damage is to understand what it is and how it’s caused.
What Moisture-Related Damage Looks Like in a Shipping Container
Water may be a necessary condition for life, but it can also cause a lot of damage. And moisture, whether as liquid water or vapor, can damage the goods trapped inside a container in multiple ways.
In some cases, it doesn’t take much moisture to produce costly damage. Excess moisture can cause packing labels to peel, which makes handling, sorting, and accounting for the boxes and their contents difficult.
More destructive types of damage can render the goods unsellable. For example, any sort of organic material is at risk for mold and mildew. From wood products to food to textiles, excessive moisture is a breeding ground for fungal growth and other growths, especially in warm climates. Dry goods, such as powders or husks, can clump or cake. Even if an organic product doesn’t show physical signs of moisture-related damage, it might develop bad odors.
Corrosion and rust can damage manufactured goods, which often include metal parts. The damage can be cosmetic, such as dulling or discoloring the metal. In more severe cases, it may disfigure or weaken the metal.
Wood especially can warp and weaken due to excessive moisture. The potential for damage doesn’t apply to the cargo alone — at least not directly. Wood or wood-based products are the primary materials used to pack and secure the cargo. Picture soggy boxes in the garage after a heavy rain or flooding. They weaken and slump. Everything stored inside them is now vulnerable to all sorts of destruction beyond moisture.
Cartons aren’t the only ways wood shows up in shipping containers. Wood beams and braces are often used to fortify fragile cargo, so it doesn’t move during shipping. If those braces get compromised due to excessive moisture, the goods can shift and break. The risks extend to goods stacked on wooden pallets.
Another way wood shows up in shipping containers is in the cushioning materials. This could be dunnage, the soft materials used to pad cartons, or soft materials within the cartons themselves. These softwood materials gobble up moisture, even when it’s still vapor. Depending on conditions within the container, these materials may never completely dry.
When thinking about the risk of moisture-related damage to a shipment, it’s necessary to think beyond the risk to the goods themselves. Excessive moisture in the wood materials that surround the cargo presents direct and indirect risks to the cargo. To understand why, let’s talk about what excess moisture can do inside a container.
How Moisture-Related Damage Occurs in a Shipping Container

Image by Dean Moriarty from Pixabay
Shipping containers are supposed to be watertight, but they are not airtight. That’s a crucial difference.
A watertight container protects its contents from spray and rain. This type of water damage can occur in an improperly sealed container. A thorough inspection of the container before and after it’s loaded can alert people to potential damage from external water sources.
It’s the moisture vapor in the air and goods in the container that is usually the real culprit. Since containers aren’t airtight, their internal temperature and relative humidity (RH) fluctuate. These environmental changes are the main cause of moisture-related damage. They provoke changes in the RH of the cargo and the air. These changes spark phenomena such as “container rain” and “cargo sweating.”
Yet before any of this can occur, moisture needs to be present in the container. The more moisture that’s available, the more likely moisture-related damage will occur to the container contents. Before breaking down how moisture can cause damage to the cargo, let’s delve into how moisture gets inside a container first.
Pooled water can get into an open container in various ways:
- spray or rain
- incomplete drying after cleaning the container’s insides
- water accidentally brought in during the loading process, say from workers’ boots
- shipping agricultural goods, most of which are packed in ice or other refrigerants
Most of the moisture within a container exists as vapor. Moisture vapor gets inside through:
- wood used to pad or brace the shipped goods, such as pallets, beams, and dunnage. Wood always contains some amount of moisture vapor. Wood with high moisture levels increases the risk of moisture-related damage.
- the goods being shipped. Many materials contain moisture vapor. Organic materials, paper goods and building materials, like tiles or moldings, hold moisture.
- high humidity in the air at the loading port, which gets trapped in the container. This is a particular issue at ports located in humid environments that don’t have climate-controlled loading docks.
Moisture vapor also enters the container during the voyage through a process called “container breathing.” But first, on to container rain.
How Container Rain Occurs
The short explanation of container rain is that cooling temperatures cause moisture vapor to convert into water. In other words, condensation. Condensation tends to accumulate on the coldest surfaces, such as the container’s ceiling. When this condensation falls onto the goods below, you have “container rain.” Condensation can accumulate on various surfaces, such as the container walls and the goods themselves.
Condensation increases the potential for moisture-related damage to occur. The moist conditions are fertile grounds for mold or bacteria to grow. It can corrode metals. It can instigate any of the moisture-related problems discussed above.
To understand how container rain occurs, think of the container as a small eco-system. It has air temperature, RH, and dew point. Changes in these environmental variables during the voyage can create condensation.
Let’s start with air temperature. Warmer air can hold more moisture than cold air. As air cools, it approaches its dew point. The air’s dew point is the temperature at which it can’t hold any more moisture as vapor. Once air drops below its dew point, the vapor in the air converts to liquid water. Some of it can be held as droplets in the air — fog. Much of it will form as condensation on surfaces.
Humidity is how much moisture there is in the air. RH is how much moisture the air is holding as a percentage of how much it can hold. RH is why cooling temperatures result in condensation.
Think about a container ship docked in Melbourne. The warm, humid air at the port in Australia can hold a lot of moisture. Now that warm, humid air gets trapped inside a container bound for Halifax. The air inside the container cools down, but its moisture levels stay the same. Since cold air can’t hold as much moisture as warmer air, the air’s RH increases.
An RH of less than 60 or 70% is unlikely to cause moisture damage. However, a climbing RH is a leading indicator that moisture-related damage may occur. For example, mold growth can start to occur when the RH hits 80% even for a short while. Some metals will start to corrode when sitting in air with an RH of 70%.
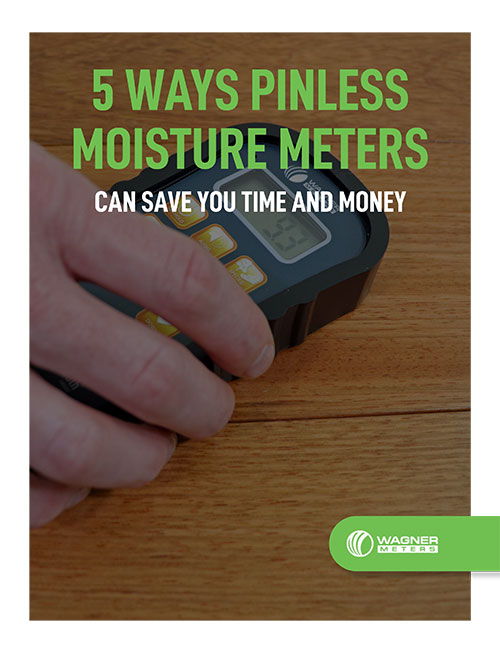
Free Download – 5 Ways Pinless Moisture Meters Save You Time and Money
How a Container “Breathes”
Remember, shipping containers aren’t airtight. Air will move back and forth between the container and its external environment.
The air starts to move when the air temperatures inside and outside the container differ. Air pressure drops as it cools. If the air inside the container is colder than the air outside, outside air will move inside to equalize the pressure. The reverse happens if the air inside the container is warmer than outside.
As the air moves, it brings its moisture vapor with it. As a result, the humidity inside the container can fluctuate. If the raw amount of moisture vapor changes, it will bring changes to the RH with it.
Air temperature changes from day to night and back to the day are enough to impact RH. Even slight changes in temperature impact air pressure, pushing air around. This is how a container breathes. As the ship moves to new climate zones, the fluctuations get more extreme.
Container breathing often results in the accumulation of more moisture vapor inside the container. Thus worsening the conditions for moisture-related damage to the goods.
Impact of RH Whether the Cargo Releases or Absorbs Moisture
The air and goods within a container aren’t all at the same temperature throughout the space. For example, the cargo may be cold while the air inside the container starts out warm. The cold cargo cools the air, increasing the air’s RH. In this case, the nearest cold surface isn’t the container ceiling, but the goods and packing materials themselves. So that’s where the excess moisture settles. This is called “cargo sweating.” These temperature variations can happen rapidly, leading the moisture absorbed into the cargo or packaging even before it forms as liquid water.
Furthermore, the varying levels of moisture within different types of goods inside the same container will experience the RH differently. Goods that are drier have a lower point of equilibrium RH and don’t release much moisture. Goods with a high moisture content won’t easily let moisture evaporate when their equilibrium RH is near the RH of the air around right them. Yet a small difference in either’s RH means moisture evaporation rate will change.
It’s not just goods that can absorb or release moisture based on the air’s RH and the goods’ equilibrium RH. If the moisture content of wood pallets on which goods are stacked is high and there’s the equilibrium of RH, the moisture of the wood can seep into those goods or degrade their packaging.
Absorbing the Costs of Moisture-Related Damage in Containerized Goods
The conventional industry understanding is that, on average, 10% of goods in a container shipping have to be discarded due to moisture-related damage.4
Whatever valuation method is used to set a dollar amount on the cargo, losing 10% on each shipment is a huge financial loss. Compare that to retail loss prevention statistics. The average inventory shrinkage, measured as a percentage of sales, is less than 2%.
Taking, on average, a loss of 10% of inventory with every voyage generates costs that companies pass to the consumer as higher prices.
That’s because it’s difficult for companies to recover those costs through insurance. Wet damage claims5 makeup around 9-10% of all shipping damage claims. Yet wet damage isn’t usually covered by insurance. The broadest type of cargo coverage clause covers “all risks.” Sounds good. But all risks coverage doesn’t include risks considered to be inevitable and for which steps can be taken to prevent, like known risks such as moisture damage due to condensation.
An all risks clause may cover water damage due to water ingress into the container. Yet this type of claim sets off a battle of “who’s responsible?” If water from a major rainstorm enters the container and damages the cargo, that’s due to some defect in the container. Is that the shipping company’s fault, the loading company’s fault, or the shipper’s fault for not inspecting the container?
The bottom line is that the company who owns the goods being shipped will nearly always bear the costs of moisture-damaged goods.
Managing Moisture-Related Problems in the Container
Moisture mitigation may seem futile with cargo sealed up on a container ship in the middle of the ocean. The key is taking steps to prevent excess moisture before that container closes.
A well-ventilated container can reduce container rain by giving high humidity a way out. Liners or certain coatings help prevent moisture accumulation on the container surfaces.
People also install moisture-management devices inside the container. These could be dehumidifiers or desiccants. A moisture-absorbing pole fits into the grooves in the container side. It has salts that absorb moisture and trap it in a gel.
Where and how the goods are stored before loading impacts how much moisture they’ll bring into the container. For example, wood pallets sitting outside will absorb the moisture in the air. Indeed, since wood is used in so many ways within a container, it’s smart to measure its moisture content before loading. That way, you can ensure the wood, whether it’s the cargo or used in the packing, is at an acceptable moisture level. Generally, wood products shouldn’t have a moisture content above 15%.
The risk for mold growth escalates if the moisture content hits 20%. Using a wood moisture meter to measure the moisture content of wood pallets and any other wood in the container (e.g., wood bracing beams or shelving) is the only way to verify that the container won’t get closed up when the wood inside it is holding too much moisture.
Another useful tool is a data logger. It doesn’t prevent moisture damage, but it can provide insight into how it happened. A data logger is a small device that shippers can leave inside the container. It continuously measures environmental conditions throughout the voyage. Wagner Meters’ Smart Logger™ tracks ambient temperature and RH data.
Shippers set how often the data logger will take a reading. They can use the data logger record to pinpoint when changes in conditions occurred. If the goods show signs of moisture-related damage, data logger information may help sort out why. Data logger records can be cross-referenced against weather data and shipping logs. This analysis builds a picture of what happened, which may be helpful in resolving some of those insurance liability questions.
Taking Moisture Seriously
It’s worth emphasizing why cargo insurance doesn’t cover most moisture-related damage: Moisture-related issues in containers are so commonplace, they’re expected. Everything inside the container has moisture that will react to environmental changes. The environment within and without the container constantly changes throughout its voyage. Worse, the changing moisture content and temperature of everything inside the container will vary. Therefore, moisture is regularly flowing from goods to the air and settling on other goods, and from the air to goods, each of which will react differently. And it’s the shipper’s responsibility to bear the cost of managing the impact of moisture on containerized goods.
A company that uses processes and tools to reduce its average loss per shipment is creating a competitive advantage for itself. Other companies will have to price goods to cover inventory loss and rebuild frayed relationships with disappointed buyers. A company with a serious moisture-management approach can run a tighter ship.
1Shipping and World Trade,” International Chamber of Shipping. Accessed on January 21, 2020. https://www.ics-shipping.org/shipping-facts/shipping-and-world-trade
2Wagner, I. “Container Shipping – Statistics & Facts,” Statista, published December 19, 2019. Accessed on January 21, 2020. https://www.statista.com/topics/1367/container-shipping/
3Lambert, Meredith, “Protect Your Cargo: How to Prevent Water Damage Within Container,” TRG blog, Trade Risk Guaranty Brokerage Services, LLC, published August 5, 2016. Accessed January 21, 2020. https://traderiskguaranty.com/trgpeak/prevent-moisture-damage-protect-cargo/
4“What Causes Container Rain?” Eurolog Packing Group, published February 26, 2019. Accessed January 21, 2020. https://www.epgna.com/causes-container-rain/
5Manaadiar, Hanriesh. “The Essential Guide to Cargo Damage,” Shipping and Freight Resource. Accessed January 21, 2020. https://shippingandfreightresource.com/wp-content/uploads/2017/10/The-Essential-Guide-to-Cargo-Damage.pdf
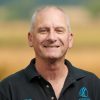
As Sales Manager for Wagner Meters, Ron has more than 35 years of experience with instrumentation and measurement systems in different industries. In previous positions, he has served as Regional Sales Manager, Product and Projects Manager, and Sales Manager for manufacturers involved in measurement instrumentation.
Related Posts via Taxonomies
Last updated on June 29th, 2022
nice post thanks for sharing